Copper-zinc-aluminum shape memory alloy abrasion resistance material and manufacturing method for the same
A technology of memory alloy and wear-resistant material, applied in the field of preparation of shape memory alloy material, can solve the problems of low yield, complex casting process, low production efficiency and the like
- Summary
- Abstract
- Description
- Claims
- Application Information
AI Technical Summary
Problems solved by technology
Method used
Image
Examples
Embodiment Construction
[0008] Electrolytic copper, 0# zinc and 00# aluminum are used as raw materials, Zn25.82%, Al3.76%, Ni0.96%, and the rest is copper. Add 0.07% compound rare earth refiner, of which: La45.5%, Ce44.9%, Pr7.7%, Nd1.9%, melted by medium frequency induction furnace, when the alloy liquid temperature reaches 1240 ℃, cast into diameter It is an ingot of φ80×150mm. The annealing treatment is to heat to 820°C for 24 hours and then cool with the furnace. Then remove the dezincification layer of 2-3mm on the surface, and then forge it to a plate with a thickness of 11mm. The alloy heat treatment process is: 850℃+150℃+50℃ two-stage aging heat treatment. The abrasion test adopts MM-200 abrasion testing machine, the size of the sample is 19.5×10×8 (mm), and the weighing adopts 1 / 10,000 photoelectric balance.
[0009] Figure 1 is the SEM photos of different copper alloys worn surfaces under the same wear conditions under 294N load. Under the same wear conditions, the wear surface of two com...
PUM
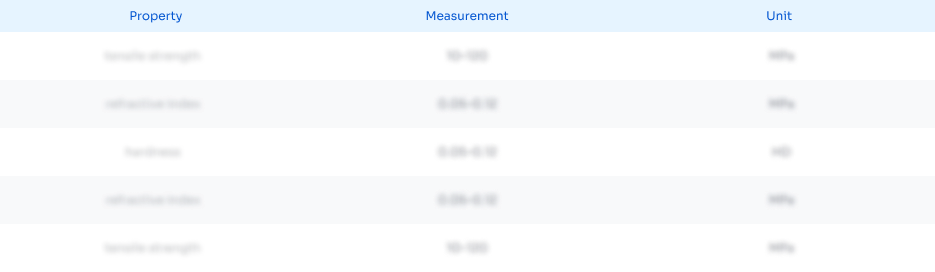
Abstract
Description
Claims
Application Information

- R&D
- Intellectual Property
- Life Sciences
- Materials
- Tech Scout
- Unparalleled Data Quality
- Higher Quality Content
- 60% Fewer Hallucinations
Browse by: Latest US Patents, China's latest patents, Technical Efficacy Thesaurus, Application Domain, Technology Topic, Popular Technical Reports.
© 2025 PatSnap. All rights reserved.Legal|Privacy policy|Modern Slavery Act Transparency Statement|Sitemap|About US| Contact US: help@patsnap.com