Activator for producing glycol by catalytic hydrogenation method
A technology for catalytic hydrogenation and catalyst, which is applied in the direction of hydrolysis preparation, etc., can solve the problems of reducing the activity of the catalyst and the proportion of pores in the catalyst is small.
- Summary
- Abstract
- Description
- Claims
- Application Information
AI Technical Summary
Problems solved by technology
Method used
Image
Examples
Embodiment 1~2
[0018] 1. In a 500mL four-neck flask equipped with a stirrer, a thermometer, and a condenser, add 22.9g of nickel-aluminum alloy with a particle size of about 1.6-2.0mm, add about 180ml of NaOH solution with a mass fraction of 10%, and keep it warm at 80°C Stir for 3 hours, and after no gas is released, wash with deionized water until neutral to obtain catalyst (a), which is stored in absolute ethanol until use. The change of aluminum content was measured, and the removal rate of aluminum was calculated to be 30%. Fill a fixed bed with an inner diameter of 10mm and a length of 4cm with 8mL of catalyst (a), for ethylene glycol with a mass concentration of 12.5%, at a bed temperature of 80°C, a hydrogen pressure of 0.05MPa, and a space velocity of 55h -1 Under the conditions of catalytic hydrogenation, the hydrogenation reaction liquid was rectified to collect the ethylene glycol fraction to obtain the ethylene glycol product. The ultraviolet light transmittance of the feed, out...
Embodiment 3~4
[0023] 3. In a 500mL four-necked flask equipped with a stirrer, a thermometer, and a condenser, add 30g of nickel-aluminum alloy with a particle size of 2.0-3.0mm, add 130mL of deionized water, raise the temperature to 85°C, and add 15% NaOH solution dropwise 80mL, control the temperature not higher than 95°C, stir at low speed for 1h, keep warm at 93°C±2°C, stand still for 2h, then add 40mL of 15% NaOH solution dropwise, stand still for 0.5h, wash with deionized water until neutral, and prepare the catalyst (b), stored in absolute ethanol until use. The change of aluminum content was measured, and the removal rate of aluminum was calculated to be 25%. Fill 12.5mL of catalyst (b) in a fixed bed with an inner diameter of 20mm and a length of 3cm. For ethylene glycol with a mass concentration of 85%, the bed temperature is 67°C, the hydrogen pressure is 0.25MPa, and the space velocity is 40h -1 Under the conditions of catalytic hydrogenation, the hydrogenation reaction liquid i...
Embodiment 5~6
[0028] 5. As in Example 3, take 12.5g of nickel-aluminum alloy with a particle size of 1.0-1.6mm, add 55mL of deionized water, raise the temperature to 85°C, add 20mL of 15% NaOH solution dropwise, control the temperature not higher than 95°C, and stir at a low speed 1h, keep warm at 93°C±2°C, let stand for 2h, then add 9.9mL of 15% NaOH solution dropwise to prepare granular catalyst (c). The change of aluminum content was measured, and the removal rate of aluminum was calculated to be 13%. Fill 2mL of catalyst (c) in a fixed bed with an inner diameter of 10mm and a length of 4cm. For ethylene glycol with a mass concentration of 85%, the bed temperature is 73°C, the hydrogen pressure is 0.25MPa, and the space velocity is 35h -1 Catalyzed hydrogenation under the conditions, hydrogenation reaction liquid rectification collects ethylene glycol fraction, obtains ethylene glycol product, and the ultraviolet light transmittance comparison of input material, output material and produ...
PUM
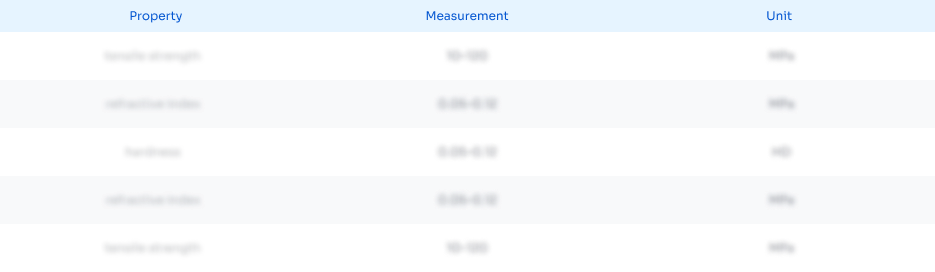
Abstract
Description
Claims
Application Information

- R&D
- Intellectual Property
- Life Sciences
- Materials
- Tech Scout
- Unparalleled Data Quality
- Higher Quality Content
- 60% Fewer Hallucinations
Browse by: Latest US Patents, China's latest patents, Technical Efficacy Thesaurus, Application Domain, Technology Topic, Popular Technical Reports.
© 2025 PatSnap. All rights reserved.Legal|Privacy policy|Modern Slavery Act Transparency Statement|Sitemap|About US| Contact US: help@patsnap.com