Residual heat generating system used for new type nonaqueous cement production line
A dry-process cement and waste heat power generation technology, which is applied in cement production, clinker production, waste heat treatment, etc., can solve problems such as air leakage, dust accumulation in heat exchangers, and uneven air distribution
- Summary
- Abstract
- Description
- Claims
- Application Information
AI Technical Summary
Problems solved by technology
Method used
Image
Examples
Embodiment Construction
[0019] As shown in Figure 1 and Figure 3, the present invention consists of a clinker cooler 1, a cement rotary kiln 2, a cement preheater 3, a cement precalciner 3', a tertiary air duct 4, a tertiary air waste heat boiler 5, a bypass Air duct 6, SP waste heat boiler 7, induced draft fan 8, deaerator 9, AQC waste heat boiler 10, kiln head electric dust collector 11, induced draft fan 12, steam turbine 13, generator 14, condenser 15, cement rotary kiln Head shield 19 forms.
[0020] Among them, the discharge end of the cement rotary kiln 2 is connected to the feed end of the clinker cooler 1 through the cement rotary kiln kiln hood 19, the feed end is connected to the cement precalciner 3', and the AQC waste heat boiler 10 is connected to the clinker cooler. 1 The air extraction port 21 opened on the side wall is connected; the waste heat pipe of the SP waste heat boiler 7 is connected with the final stage outlet of the cement preheater 3; the working medium outlet of the AQC w...
PUM
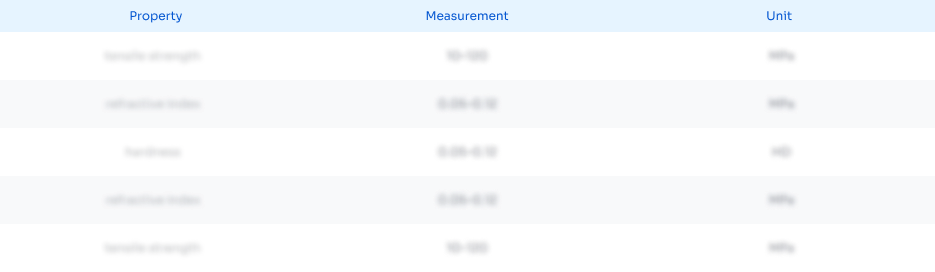
Abstract
Description
Claims
Application Information

- R&D
- Intellectual Property
- Life Sciences
- Materials
- Tech Scout
- Unparalleled Data Quality
- Higher Quality Content
- 60% Fewer Hallucinations
Browse by: Latest US Patents, China's latest patents, Technical Efficacy Thesaurus, Application Domain, Technology Topic, Popular Technical Reports.
© 2025 PatSnap. All rights reserved.Legal|Privacy policy|Modern Slavery Act Transparency Statement|Sitemap|About US| Contact US: help@patsnap.com