Redundant electrohydraulic servo-controlling system
An electro-hydraulic servo and control system technology, applied in the field of electro-hydraulic servo systems, can solve problems such as insufficient flow of electro-hydraulic servo control systems, achieve the effects of reducing energy consumption, ensuring reliable operation, and improving controllability
- Summary
- Abstract
- Description
- Claims
- Application Information
AI Technical Summary
Problems solved by technology
Method used
Image
Examples
Embodiment 1
[0019] Such as figure 1 , the hydraulic pump 1, the motor 2, the relief valve 3 and the accumulator 4 constitute the hydraulic oil source, the output shaft of the motor 2 is connected with the input shaft of the hydraulic pump 1 through a coupling, and the oil inlet of the hydraulic pump 1 is connected through a pipeline Connected to the oil tank, the oil outlet of the hydraulic pump 1 passes through the fifth hydraulic line l 5 Output, as the output of the oil source, the oil inlet of the relief valve 3 passes through the fifth hydraulic line l 5 It is connected to the oil outlet of the hydraulic pump 1, the oil return port of the relief valve 3 is connected to the oil tank, and the oil port of the accumulator 4 passes through the fifth hydraulic pipeline l 5 Connected to the output port of the oil source; the first oil outlet A1 of the servo valve I5 passes through the first hydraulic line l 1 , two-position two-way solenoid valve I15, the third hydraulic pipeline l 3 It ...
Embodiment 2
[0022] Such as figure 1 , the connection mode and structural principle of this embodiment are the same as those in Embodiment 1, and the two-position two-way solenoid valve I15 and the two-position two-way solenoid valve II16 are connected at the same time, and the maximum movement speed of the load 14 in the left and right directions in the figure Respectively reach twice the single servo valve control. Realize high-speed response control to the load.
Embodiment 3
[0024] Such as figure 2 , connect the two-position two-way solenoid valve I15, and the hydraulic actuator 9 moves in one direction (moving to the right in the figure). Double servo valve I5 and servo valve II6 are used to supply oil, while the hydraulic actuator moves in the other direction (see figure middle to left movement) adopts single servo valve I5 to supply oil. This method is used to increase the one-way flow rate of the hydraulic actuator 9 and is suitable for balancing the movement speed of the asymmetric hydraulic actuator 9 in two directions.
PUM
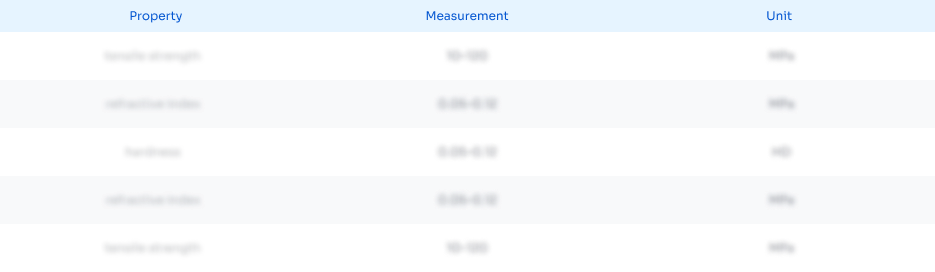
Abstract
Description
Claims
Application Information

- R&D
- Intellectual Property
- Life Sciences
- Materials
- Tech Scout
- Unparalleled Data Quality
- Higher Quality Content
- 60% Fewer Hallucinations
Browse by: Latest US Patents, China's latest patents, Technical Efficacy Thesaurus, Application Domain, Technology Topic, Popular Technical Reports.
© 2025 PatSnap. All rights reserved.Legal|Privacy policy|Modern Slavery Act Transparency Statement|Sitemap|About US| Contact US: help@patsnap.com