Recycling method for recovering metal type powder coating
A technology of powder coating and metal molding, applied in the direction of powder coating, etc., can solve the problems that the recycled powder cannot be reused, destroys the composition ratio of the powder, and has a complex structure, so as to achieve great social and economic benefits, solve processing problems, and avoid pollution environmental effects
- Summary
- Abstract
- Description
- Claims
- Application Information
AI Technical Summary
Problems solved by technology
Method used
Examples
Embodiment 1
[0013] Add 33.3Kg of base powder to the batching tank (the content of each component: 21.65Kg of pure polyester; 4.66Kg of barium sulfate solid; 4.66Kg of titanium dioxide; 1.50Kg of curing agent; 0.4Kg of pigment; 0.26Kg of leveling agent; 701 doses 0.07Kg; Benzoin 0.1Kg), and then take an appropriate amount of metal-type powder coating recycled powder, after sieving, take 66.7Kg recycled powder and add it to the batching tank, stir evenly with a high-speed machine, and the time does not exceed 30 seconds to obtain new powder.
Embodiment 2
[0015] Add base powder 28.5Kg (wherein the content of each component: pure polyester 18.53Kg; barium sulfate solid 3.99Kg; titanium self-powder 3.99Kg; curing agent 1.28Kg; pigment 0.34Kg; leveling agent 0.22Kg; 701 Benzoin 0.06Kg; Benzoin 0.09Kg), and then take an appropriate amount of metal-type powder coating recycled powder, after sieving, take 71.5Kg recycled powder and add it to the batching tank, stir evenly with a high-speed machine, and the new powder will be obtained within 30 seconds .
Embodiment 3
[0017] Add 25.0Kg of base powder to the batching tank (the content of each component: pure polyester 16.25Kg; barium sulfate solid 3.50Kg; titanium dioxide 3.50Kg; curing agent 1.13Kg; pigment 0.3Kg; leveling agent 0.2Kg; 701 doses 0.05Kg; Benzoin 0.07Kg), and then take an appropriate amount of recycled metal-type powder coating powder, after sieving, take 75.0Kg of recycled powder and add it to the batching tank, and stir evenly with a high-speed machine for no more than 30 seconds to obtain new powder.
[0018] In the method of the invention, the metal powder utilization rate reaches over 95%.
PUM
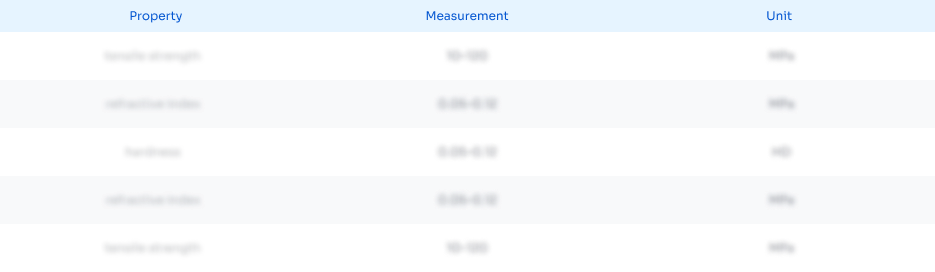
Abstract
Description
Claims
Application Information

- R&D Engineer
- R&D Manager
- IP Professional
- Industry Leading Data Capabilities
- Powerful AI technology
- Patent DNA Extraction
Browse by: Latest US Patents, China's latest patents, Technical Efficacy Thesaurus, Application Domain, Technology Topic, Popular Technical Reports.
© 2024 PatSnap. All rights reserved.Legal|Privacy policy|Modern Slavery Act Transparency Statement|Sitemap|About US| Contact US: help@patsnap.com