Method for fast preparing lamellate potassium titanate
A kind of potassium titanate, layered technology, applied in the field of preparing layered potassium titanate salt
- Summary
- Abstract
- Description
- Claims
- Application Information
AI Technical Summary
Problems solved by technology
Method used
Image
Examples
Embodiment 1
[0018] Step 1 Melt and mix, take the reactant of potassium stearate and butyl titanate with a potassium-titanium molar ratio of 1:2: 16.13g potassium stearate and 34.03g butyl titanate; add butyl titanate to the molten state In the potassium stearate, add 60g of stearic acid as a solvent to ensure uniform mixing, and the heating and stirring time is 0.5h; if the reactant exceeds 200g, do not add stearic acid solvent.
[0019] Step 2 Combustion in an electric furnace, put the mixture obtained in step 1 into a beaker, place it on an electric furnace with a power of 1kW, heat it to the ignition point, and burn for 2h.
[0020] Step 3: Roasting. The electric furnace combustion product in step 2 is fully ground, put into a muffle furnace, and heated to 750°C at a heating rate of 15°C / min for roasting to obtain layered potassium titanate.
[0021] The resulting layered potassium titanate has the molecular formula K 2 Ti 4 o 9 .
Embodiment 2
[0023] Step 1 Melt and mix, the reactant of potassium stearate and butyl titanate with a potassium-titanium molar ratio of 1:2: 16.13g potassium stearate and 34.03g butyl titanate; add butyl titanate to the molten state In the potassium stearate, add 60g of stearic acid as a solvent to ensure uniform mixing, and the heating and stirring time is 0.5h; if the reactant exceeds 200g, do not add stearic acid solvent.
[0024] Step 2 Combustion in an electric furnace, put the mixture obtained in step 1 into a beaker, place it on an electric furnace with a power of 1kW, heat it to the ignition point, and burn for 2h.
[0025] Step 3 roasting, fully grind the electric furnace combustion product in step 2, put it into a muffle furnace, heat it to 800 °C at a heating rate of 15 °C / min and roast for 2.5 hours to obtain layered potassium titanate.
[0026] The resulting layered potassium titanate has the molecular formula K 2 Ti 4 o 9 .
Embodiment 3
[0028] Step 1 Melt and mix, the reactant of potassium stearate and butyl titanate with a potassium-titanium molar ratio of 1:2: 170.15 g of butyl titanate is added to 80.65 g; butyl titanate is added to the molten stearin Potassium acid, the heating and stirring time is 0.5h.
[0029] Step 2 Combustion in an electric furnace, put the mixture obtained in step 1 into a beaker, place it on an electric furnace with a power of 1kW, heat it to the ignition point, and burn for 2h;
[0030] Step 3 roasting, fully grind the electric furnace combustion product in step 2, put it into a muffle furnace, heat it up to 800 °C at a heating rate of 15 °C / min and roast for 2.5 hours to obtain layered potassium titanate.
[0031] The resulting layered potassium titanate has the molecular formula K 2 Ti 4 o 9 .
[0032] figure 1 It is the X-ray diffraction pattern of the product obtained by the method at the calcination temperature of 750°C and 800°C. It can be clearly seen that no other in...
PUM
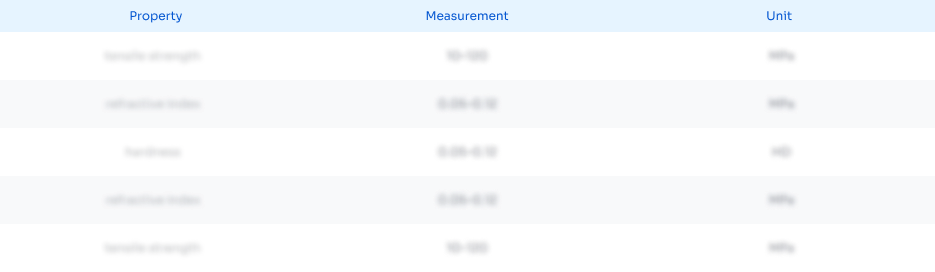
Abstract
Description
Claims
Application Information

- R&D Engineer
- R&D Manager
- IP Professional
- Industry Leading Data Capabilities
- Powerful AI technology
- Patent DNA Extraction
Browse by: Latest US Patents, China's latest patents, Technical Efficacy Thesaurus, Application Domain, Technology Topic.
© 2024 PatSnap. All rights reserved.Legal|Privacy policy|Modern Slavery Act Transparency Statement|Sitemap