Dynamic injecting system of injection moulder, and its vibration injecting method
An injection molding machine and dynamic technology, applied in the field of polymer dynamic injection, can solve the problems that the screw rod cannot realize large thrust drive, cannot realize large thrust movement, and increase equipment investment, etc. low cost effect
- Summary
- Abstract
- Description
- Claims
- Application Information
AI Technical Summary
Problems solved by technology
Method used
Image
Examples
Embodiment
[0029] The specific structure of the present invention is as Figure 5 to Figure 9 shown by Figure 5 and Figure 6 It can be seen that the dynamic injection system of the injection molding machine includes an injection barrel 1, a screw 2, and an injection drive mechanism. The screw 2 extends into the injection barrel 1, and the injection drive mechanism is a crank vibration injection mechanism. The ends are connected; the crank vibration injection mechanism is as Figure 7 ~ Figure 9 As shown, it includes three crank drive assemblies, and the three crank drive assemblies are arranged in phases of 120° (see Figure 9 ), and is connected with the synchronous drive, and the synchronous drive simultaneously drives each crank drive assembly to move 120° phase cycle, the synchronous drive can be the drive shaft 3 of the same motor, and the crank drive assembly is as Figure 7 and Figure 8 As shown, it includes an injection plunger barrel 4, a plunger 5, and a crank assembly 6...
PUM
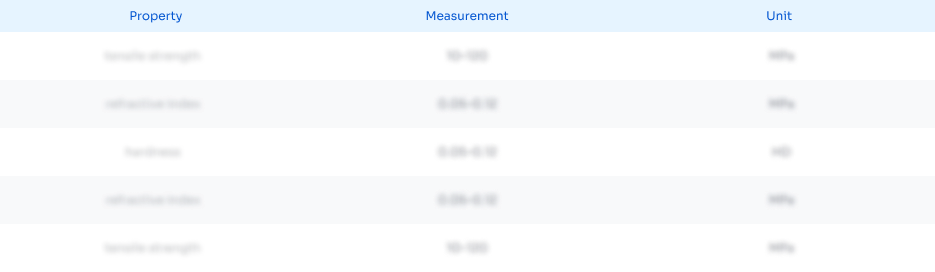
Abstract
Description
Claims
Application Information

- R&D Engineer
- R&D Manager
- IP Professional
- Industry Leading Data Capabilities
- Powerful AI technology
- Patent DNA Extraction
Browse by: Latest US Patents, China's latest patents, Technical Efficacy Thesaurus, Application Domain, Technology Topic, Popular Technical Reports.
© 2024 PatSnap. All rights reserved.Legal|Privacy policy|Modern Slavery Act Transparency Statement|Sitemap|About US| Contact US: help@patsnap.com