Process for producing benzal chloride or chloro benzal chloride
A technology of chlorinated benzylidene dichloride and benzylidene dichloride, which is applied in the field of producing benzylidene dichloride or chlorinated benzylidene dichloride, can solve the problems of complex composition of leftovers, small amount of leftovers, poor product quality, etc. Achieve the effect of low production cost, high conversion rate and high economic benefit
- Summary
- Abstract
- Description
- Claims
- Application Information
AI Technical Summary
Problems solved by technology
Method used
Image
Examples
Embodiment 1
[0031] use as figure 1 In the process flow shown, the number of reactors coupled with the rectification tower is 3. Benzyl chloride and chlorine feed are both 1.4kmol / h, the distribution ratio of chlorine in the three reactors is: 0.45:0.32:0.23, the tower top condensation is 1000L / h, and the temperature of the chlorination reactor is 95°C. The operating pressure of the rectification tower is 0.025MPa, the number of trays in the rectification zone is 9, and the number of trays in the separation zone is 30. After reactive distillation, the molar composition of the tower kettle is: 0.1% benzyl chloride, 99.4% benzylidene dichloride, 0.45% benzyl trichloride, and 0.05% cyclodichlorotoluene.
Embodiment 2
[0033] use as figure 2 In the process flow shown, there is one pre-chlorination reactor, and the number of reactors coupled with the rectification tower is 3. The toluene feed is 1.4kmol / h, the chlorine feed is 2.8kmol / h, the distribution ratio of chlorine in the four reactors is 0.65:0.15:0.1:0.1, and the condensation at the top of the tower is 1000L / h, the chlorination reactor The temperature is 80°C, the operating pressure of the rectification tower is 0.05 MPa, the number of trays in the rectification zone is 6, and the number of trays in the separation zone is 25. After reactive distillation, the molar composition of the tower kettle is: 0.2% benzyl chloride, 99.1% benzylidene dichloride, 0.55% benzyl trichloride, and 0.05% cyclodichlorotoluene.
Embodiment 3
[0035] use as figure 1 In the process flow shown, the number of reactors coupled with the rectification tower is 3. O-chlorobenzyl chloride and chlorine are both 1.4kmol / h, the distribution ratio of chlorine in the three reactors is: 0.5:0.3:0.2, the condensation at the top of the tower is 1300L / h, and the temperature of the chlorination reactor is 120°C. The operating pressure of the rectification tower is 0.002MPa, the number of trays in the rectification zone is 6, and the number of trays in the separation zone is 20. After reactive distillation, the molar composition of the tower kettle is: 0.15% o-chlorobenzyl chloride, 99.15% o-chlorobenzylidene dichloride, 0.55% o-chlorobenzyl trichloride, and 0.15% cyclodichlorotoluene.
PUM
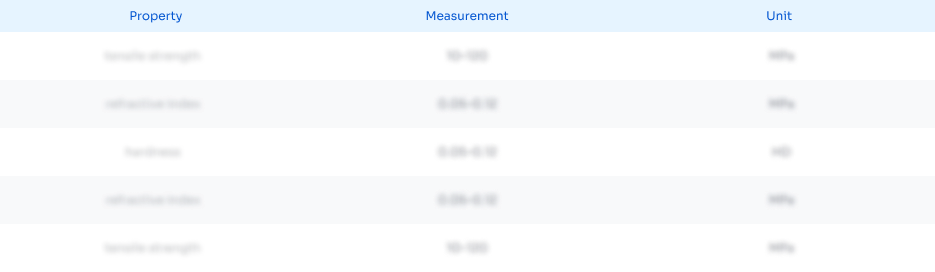
Abstract
Description
Claims
Application Information

- Generate Ideas
- Intellectual Property
- Life Sciences
- Materials
- Tech Scout
- Unparalleled Data Quality
- Higher Quality Content
- 60% Fewer Hallucinations
Browse by: Latest US Patents, China's latest patents, Technical Efficacy Thesaurus, Application Domain, Technology Topic, Popular Technical Reports.
© 2025 PatSnap. All rights reserved.Legal|Privacy policy|Modern Slavery Act Transparency Statement|Sitemap|About US| Contact US: help@patsnap.com