Gas injection boiler using the emulsifying coke mortar combustion device
A technology of a combustion device and a steam injection boiler, which is applied to steam boilers, water-tube steam boilers, and combustion with various fuels, etc., can solve the problems of not reaching the melting point of emulsified coke slurry ash, ash, high manufacturing cost, and energy waste. , to achieve the effect of continuous and effective liquid slag removal, reduction of nitrogen oxides, efficient and stable combustion
- Summary
- Abstract
- Description
- Claims
- Application Information
AI Technical Summary
Problems solved by technology
Method used
Image
Examples
Embodiment 1
[0052] Please refer to figure 1 and figure 2 , The steam injection boiler of the present invention includes a boiler body and an emulsified coke slurry combustion device. The boiler body includes a furnace 402, a steam pipe 405 coiled in the furnace 402, and a smoke outlet 408 on one end wall of the furnace 402 away from the emulsified coke slurry combustion device. The emulsified coke slurry combustion device includes a casing 10, an emulsified coke slurry burner 70, an oil burner (not shown), and a gas burner (not shown). The emulsified coke slurry combustion device is in communication with the furnace 402.
[0053] Wherein, the steam pipe 405 extends from the furnace 402 to the side wall of the emulsified coke slurry combustion device and then folds back into the furnace 402. In this embodiment, the steam pipe 405 is folded back fifteen times in the side wall of the emulsified coke slurry combustion device. Specifically, those portions of the steam pipe 405 in the side wall a...
Embodiment 2
[0074] Please refer to Figure 5 and Figure 6 As another embodiment of the present invention, it is similar to Example 1, except that:
[0075] The opening area of the liquid slag outlet 66 on the inner wall of the side wall 60 is approximately equal to one twentieth of the cross-sectional area of the combustion space 30.
[0076] The vertical distance between the inner wall of the front end wall 20 and the inner wall of the rear end wall 40 is 1.5 times the inner diameter of the combustion space 30.
[0077] The diameter of the outlet 44 is approximately equal to one-half of the inner diameter of the combustion space 30, and a conical transition chamber 48 is formed between the outlet 44 and the side wall 60 of the casing 10. That is, a flared opening is formed in the rear end wall 40.
[0078] There are four emulsified coke slurry burners 70. The four emulsified coke slurry burners 70 are respectively installed on the front end wall 20 and are distributed at equal intervals...
Embodiment 3
[0086] As another implementation manner of the present invention, it is similar to Example 1, except that:
[0087] The boiler body includes three steam pipes 405 coiled in the furnace 402, and each steam pipe 405 is folded five times in the side wall 60 of the emulsified coke slurry combustion device.
[0088] The steam injection boiler using the emulsified coke slurry combustion device is provided with two spaced apart liquid slag outlets 66 of the same size. The opening area of each liquid slag outlet 66 on the inner wall of the side wall 60 is approximately equal to the cross-sectional area of the combustion space. One-thirtieth.
[0089] The two liquid slag outlets 66 are surrounded by the same transition cavity 666 and connected to the slag containing space of the same slag discharge truck 500.
[0090] The vertical distance between the inner wall of the rear end wall 40 and the inner wall of the front end wall 20 is 4 times the inner diameter of the combustion space 30....
PUM
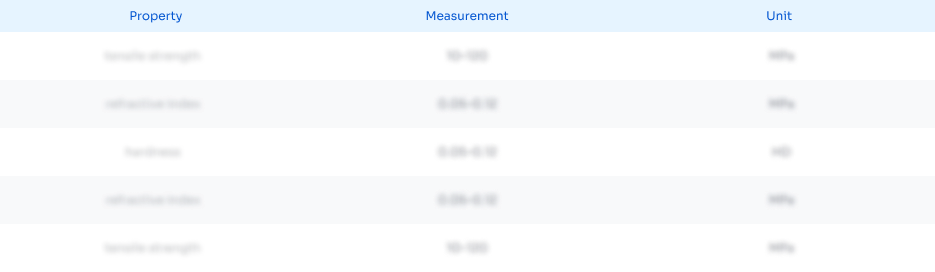
Abstract
Description
Claims
Application Information

- R&D
- Intellectual Property
- Life Sciences
- Materials
- Tech Scout
- Unparalleled Data Quality
- Higher Quality Content
- 60% Fewer Hallucinations
Browse by: Latest US Patents, China's latest patents, Technical Efficacy Thesaurus, Application Domain, Technology Topic, Popular Technical Reports.
© 2025 PatSnap. All rights reserved.Legal|Privacy policy|Modern Slavery Act Transparency Statement|Sitemap|About US| Contact US: help@patsnap.com