Rock engaged combined pile and its construction method
A technology of combining piles and pile sections, which is applied in the direction of sheet pile walls, foundation structure engineering, construction, etc., can solve the problems of increased pile cap thickness, reduced bearing capacity, and increased construction cost, and achieves the improvement of single pile bearing capacity, contact The effect of increasing the area and improving the matching degree
- Summary
- Abstract
- Description
- Claims
- Application Information
AI Technical Summary
Problems solved by technology
Method used
Image
Examples
no. 1 example
[0057] Such as figure 1 Shown is the whole pile sectional view of the first embodiment of the present invention (subclass 1 shown in the table). 100 in the figure is the soil layer, 200 is the stone layer, H1 is the design elevation of the pile head, H2 is the elevation of the rock top surface, H0 is the pile head according to the specific design, HA is the anchorage height of the steel bar, and HP is the grouting height according to the design requirements . The pile section in the soil layer is a concrete prefabricated casing pile 1, and the pile section in the rock hole uses an outer reinforcement cage 5 and an inner reinforcement cage 4 to form a member with a large surface area and fully contacted with the grouting material 12. 6 in the figure is the stirrup of the outer cage, 7 is the vertical member of the inner cage, and 3 is a flange made of annular steel plate, which is connected to the outer reinforcement cage 5 and the prefabricated cage by welding (including butt...
no. 2 example
[0062] Figure 4 It is a sectional view of the whole pile of the second embodiment of the combined pile of the present invention, which combines subclass 1 and subclass 2 shown in the table. The second embodiment is composed of the hollow prefabricated pipe 1 in the soil layer 100, the cast-in-place pile body formed by adding the section steel 21 in the stone layer 200, and the inner reinforcement cage 4 grouted. The pile sections in the soil layer 100 are the same as those in the first embodiment, and will not be repeated here. The pile section in the stone layer 200 is made of section steel 21 and optionally provided with an inner reinforcement cage 4 according to the specific design. At the same time, an annular connecting plate 3 and a selective reinforcement member 13 are used, so that the load from the upper hollow pipe 1 can be transmitted smoothly steel 21, so the role of the reinforcing member 13 is to expand the contact surface between the steel 21 and the connectin...
no. 3 example
[0066] Figure 7 Shown is the whole pile sectional view of the third embodiment of the composite pile of the present invention. The third embodiment shows subclass 3 in the table; it can be seen that the pile body in the soil layer 100 of this embodiment is the same as that of the first two embodiments, that is, the grout 12 is not poured to the top of the pipe pile member 1 . And the pile body being in the rock hole 201 is a prefabricated reinforced concrete member, which is a prefabricated multifaceted pipe 14 in the shape of a truncated cone with a small head downward, in fact it can be designed as a pipe or column of any shape with a concave-convex surface Body, the purpose is to improve the bonding force between it and the filling material. The center of the tapered prefabricated pipe 14 has a stepped hole through both ends, and the top of the stepped hole is a large diameter hole to reduce the transport weight of the prefabricated part and strengthen the integrity of t...
PUM
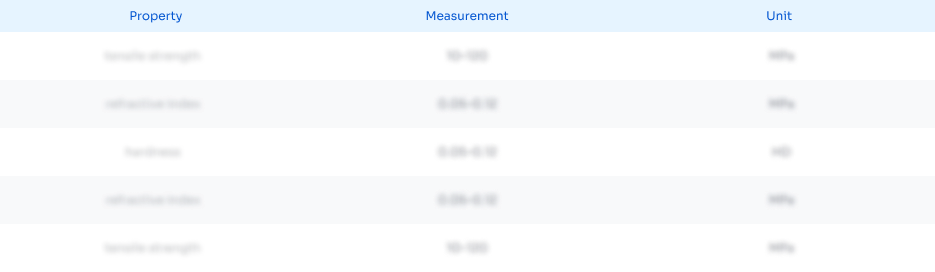
Abstract
Description
Claims
Application Information

- R&D
- Intellectual Property
- Life Sciences
- Materials
- Tech Scout
- Unparalleled Data Quality
- Higher Quality Content
- 60% Fewer Hallucinations
Browse by: Latest US Patents, China's latest patents, Technical Efficacy Thesaurus, Application Domain, Technology Topic, Popular Technical Reports.
© 2025 PatSnap. All rights reserved.Legal|Privacy policy|Modern Slavery Act Transparency Statement|Sitemap|About US| Contact US: help@patsnap.com