Process of producing nitrobenzether aminobenzether amidobenzether from chlorobenzene
A technology of amidophenylene ether and nitrophenylene ether, which is applied in the preparation of amino hydroxyl compounds, nitro compounds, carboxylic acid amides, etc., can solve the problems of large amount of three wastes, difficulty in treatment, high separation cost, etc., and achieve production cost Low, high production stability and safety effect
- Summary
- Abstract
- Description
- Claims
- Application Information
AI Technical Summary
Problems solved by technology
Method used
Image
Examples
Embodiment 1
[0052] A clean production of o-nitroanisole, p-nitroanisole, anthranil, p-aminoanisole, 2,4-dinitroanisole, 2,4- The technique of diaminoanisole and 2-amino-4-acetamidoanisole, described processing step is as follows:
[0053] (1). Nitration reaction, using chlorobenzene as raw material, chlorobenzene is subjected to adiabatic nitration by mixed acid composed of nitric acid and sulfuric acid in a static mixed nitration reactor to obtain a mixture of nitrochlorobenzene, and the dehydration value of the mixed acid is between 2.0-3.2 Between, the ratio of chlorobenzene to nitric acid is 1:1.05. Continuous adiabatic nitration reaction occurs in continuous static mixer adiabatic nitration reactor. mixed with water
[0054] (2). Evaporation and concentration, after continuous adiabatic nitration reaction, the material is decompressed to 98.0kPa, water and residual nitric acid are distilled off, and then liquid-liquid separation;
[0055] (3). Liquid-liquid separation. The evaporat...
PUM
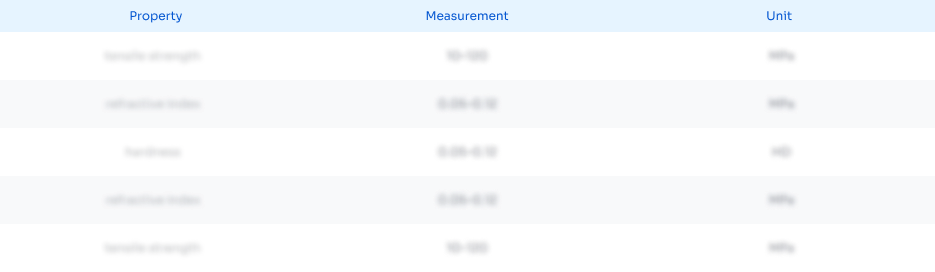
Abstract
Description
Claims
Application Information

- Generate Ideas
- Intellectual Property
- Life Sciences
- Materials
- Tech Scout
- Unparalleled Data Quality
- Higher Quality Content
- 60% Fewer Hallucinations
Browse by: Latest US Patents, China's latest patents, Technical Efficacy Thesaurus, Application Domain, Technology Topic, Popular Technical Reports.
© 2025 PatSnap. All rights reserved.Legal|Privacy policy|Modern Slavery Act Transparency Statement|Sitemap|About US| Contact US: help@patsnap.com