TiAl/Ti2AlN intermetallic compound composite material and its preparing method
An intermetallic compound and composite material technology, which is applied in the field of preparation of TiAl intermetallic compound materials, can solve the problems of material performance barriers, difficulty in eliminating pores, and difficulty in the distribution of ceramic phase particles, and achieves high adjustability and low cost. , The effect of uniform and dense structure
- Summary
- Abstract
- Description
- Claims
- Application Information
AI Technical Summary
Problems solved by technology
Method used
Image
Examples
Embodiment 1
[0011] Embodiment 1, at first by mass percentage 37% Ti, 63% Al are made mixture; Add the sodium stearate dispersant of mixture quality 0.5% in the mixture, adopt dry process ball milling in planetary ball mill with 800 revolutions The rotation speed per minute, the mass ratio of material to ball is 1:10, and the ball milling time is 27 hours to make it mechanically alloyed to form fine amorphous powder; dry the alloyed amorphous powder at 70°C for 4 hours; Put the powder into a graphite grinding tool, and heat-press and sinter at 1200°C and 28MPa pressure for 1.5 hours under argon or vacuum conditions. The obtained composite material is composed of matrix phase and reinforcement phase, and the matrix phase is composed of TiAl phase and Ti 3 Al phase composition, reinforcement phase is Ti 2 AlN. see figure 1 , figure 1 The XRD analysis results of the alloyed powder sintered at 1200°C show that the main crystal phases are TiAl and Ti 2 AlN phase and a small amount of Ti 3...
Embodiment 2
[0012] Embodiment 2, at first 84% Ti, 16% Al are made into mixture by mass percentage; Add the sodium stearate dispersant of mixture quality 0.3% in the mixture, adopt dry process ball milling in planetary ball mill with 780 turns The rotation speed per minute, the mass ratio of the material to the ball is 1:10, and the ball milling time is 25 hours to make it mechanically alloyed to form a fine amorphous powder; dry the alloyed amorphous powder at 76°C for 5 hours; Put the powder into a graphite grinding tool, and heat-press and sinter at 1000°C and 35MPa pressure for 2.0 hours under argon or vacuum conditions.
Embodiment 3
[0013] Embodiment 3, at first 50% Ti, 50% Al are made mixture by mass percentage; Add the sodium stearate dispersant of mixture quality 0.2% in the mixture, adopt dry process ball milling in planetary ball mill with 720 turns The rotation speed per minute, the mass ratio of the material to the ball is 1:10, and the ball milling time is 26 hours to make it mechanically alloyed to form a fine amorphous powder; dry the alloyed amorphous powder at 72°C for 4.3 hours; Put the powder into a graphite grinding tool, and sinter it under argon or vacuum at 950°C and a pressure of 17MPa for 2.5 hours.
PUM
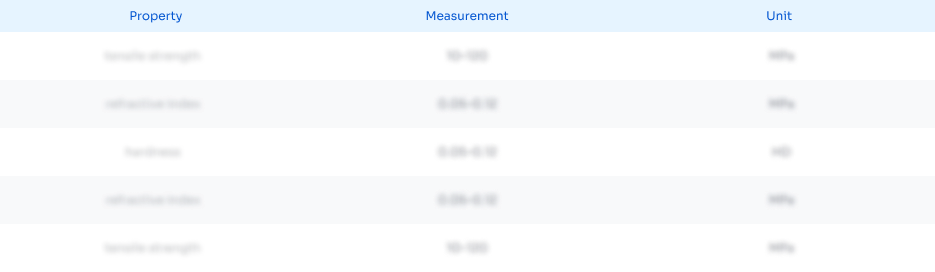
Abstract
Description
Claims
Application Information

- R&D
- Intellectual Property
- Life Sciences
- Materials
- Tech Scout
- Unparalleled Data Quality
- Higher Quality Content
- 60% Fewer Hallucinations
Browse by: Latest US Patents, China's latest patents, Technical Efficacy Thesaurus, Application Domain, Technology Topic, Popular Technical Reports.
© 2025 PatSnap. All rights reserved.Legal|Privacy policy|Modern Slavery Act Transparency Statement|Sitemap|About US| Contact US: help@patsnap.com