Laser machining apparatus for main-bearing cracker of engine cylinder
A technology of engine cylinder block and main bearing seat, which is applied in metal processing equipment, laser welding equipment, welding equipment, etc., can solve the problems of affecting the processing accuracy of cracking tank, affecting the quality of cracking processing, increasing cracking force, etc., and achieves small deformation. , The effect of reducing the slag phenomenon and improving the machining accuracy
- Summary
- Abstract
- Description
- Claims
- Application Information
AI Technical Summary
Problems solved by technology
Method used
Image
Examples
Embodiment Construction
[0031] The following embodiments are given in conjunction with the accompanying drawings to further describe the device of the present invention in detail.
[0032] Referring to Fig. 4, a laser processing equipment for cracking grooves of engine block main bearings includes a mechanical system and a YAG solid laser cutting system. It is characterized in that the mechanical system is composed as follows:
[0033] Above the workbench frame 4, there is a two-axis numerically controlled workbench that can translate along the X and Y axes (the X axis is the direction perpendicular to the drawing surface, and the Y axis is the horizontal direction of the drawing surface). Laser cutting head rotary oil cylinder 9 is arranged. The laser cutting head 2 is connected with the rotary oil cylinder 9 through the support sleeve 11 .
[0034] The engine cylinder block 14 is accurately positioned above the cylinder body frame 3 through the positioning pin 12 and the positioning oil cylinder ...
PUM
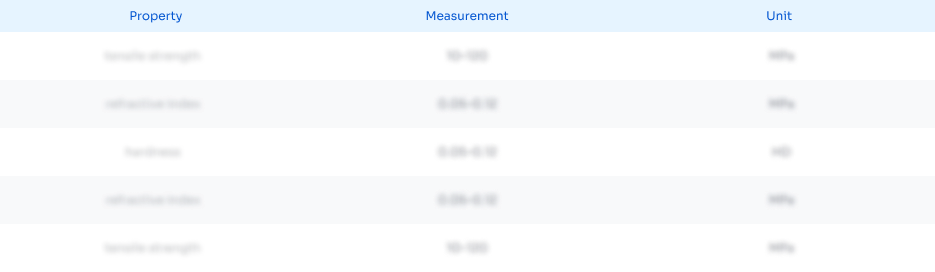
Abstract
Description
Claims
Application Information

- R&D Engineer
- R&D Manager
- IP Professional
- Industry Leading Data Capabilities
- Powerful AI technology
- Patent DNA Extraction
Browse by: Latest US Patents, China's latest patents, Technical Efficacy Thesaurus, Application Domain, Technology Topic, Popular Technical Reports.
© 2024 PatSnap. All rights reserved.Legal|Privacy policy|Modern Slavery Act Transparency Statement|Sitemap|About US| Contact US: help@patsnap.com