Continuous long fiber reinforced fire-retardant thermoplastic resin and its preparation
A thermoplastic resin and reinforced thermoplastic technology, applied in the field of continuous long fiber reinforced flame retardant thermoplastic resin and its preparation, can solve the problems of unguaranteed product quality, low production efficiency, limitation of pultrusion speed, etc. High efficiency and cost saving effect
- Summary
- Abstract
- Description
- Claims
- Application Information
AI Technical Summary
Problems solved by technology
Method used
Examples
Embodiment 1
[0027] Nylon 66 (PA66) resin is made of continuous glass fiber reinforced PA66 resin masterbatch with a glass fiber content of 60% by pultrusion process; 75% nylon 6 (PA6) resin, 12% red phosphorus, 10% magnesium hydroxide, 1% PTFE, 1% E wax, 0.5% 1098 antioxidant and 0.5% 168 antioxidant are mixed, and the PA6 flame retardant masterbatch is made by traditional extrusion process. Then, the continuous glass fiber reinforced PA66 resin masterbatch and PA6 flame retardant masterbatch were blended at a ratio of 1:1, and injection molded into standard mechanical and combustion test specimens for testing. In the final continuous glass fiber reinforced flame retardant PA66 / PA6 alloy resin, it contains 20% PA66 resin, 37.5% PA6 resin, 6% red phosphorus, 5% magnesium hydroxide, 30% long glass fiber, 0.5% E wax, 0.5% PTFE, 0.25% 1098 and 0.25% 168.
Embodiment 2
[0029]Nylon 6 (PA6) resin is made of continuous glass fiber reinforced PA6 resin masterbatch with a glass fiber content of 75% by pultrusion process; 51% nylon 6 resin, 35% polybrominated styrene, 12% antimony oxide, 1 % PTFE, 0.5% 1098 antioxidant and 0.5% 168 antioxidant are mixed, and the PA6 flame retardant masterbatch is made by traditional extrusion process. Then, the continuous glass fiber reinforced nylon 6 resin masterbatch and nylon 6 flame retardant masterbatch were blended at a ratio of 2:3, and injection molded into standard mechanical and combustion test specimens for testing. In the final continuous glass fiber reinforced flame retardant PA6 resin, it contains 40.6% PA6 resin, 21% polybrominated styrene, 7.2% antimony oxide, 30% long glass fiber, 0.6% polytetrafluoroethylene, 0.3% 1098 and 0.3% 168.
Embodiment 3
[0031] Polybutylene terephthalate resin (PBT) adopts pultrusion process to make the glass fiber content is the continuous glass fiber reinforced PBT resin masterbatch of 50%; 50% polybutylene terephthalate resin, 35% brominated polycarbonate, 12% antimony oxide, 1% polytetrafluoroethylene, 1% pentaerythritol tetrastearate, 0.5% 1010 antioxidant and 0.5% 168 antioxidant mixed, made by traditional extrusion process into PBT flame retardant masterbatch. Then, the continuous glass fiber reinforced PBT resin masterbatch and PBT flame retardant masterbatch were blended at a ratio of 3:2, and injection molded into standard mechanical and combustion test specimens for testing. In the final continuous glass fiber reinforced flame retardant PBT resin, it contains 50% PBT resin, 14% brominated polycarbonate, 4.8% antimony oxide, 30% long glass fiber, 0.4% pentaerythritol tetrastearate, 0.4% polytetrafluoroethylene Vinyl fluoride, 0.2% 1010 and 0.2% 168.
PUM
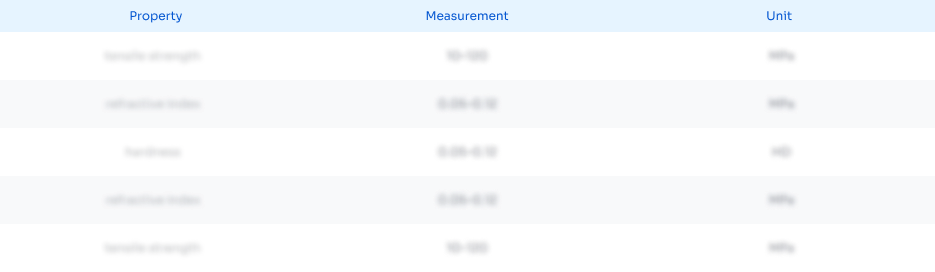
Abstract
Description
Claims
Application Information

- R&D Engineer
- R&D Manager
- IP Professional
- Industry Leading Data Capabilities
- Powerful AI technology
- Patent DNA Extraction
Browse by: Latest US Patents, China's latest patents, Technical Efficacy Thesaurus, Application Domain, Technology Topic, Popular Technical Reports.
© 2024 PatSnap. All rights reserved.Legal|Privacy policy|Modern Slavery Act Transparency Statement|Sitemap|About US| Contact US: help@patsnap.com