Manufacturing method for chromatic filter layer
A technology for a color filter layer and a manufacturing method, which is applied in semiconductor/solid-state device manufacturing, optics, nonlinear optics, etc., can solve the problems such as difficulty in adjusting the alignment accuracy of the color filter layer, decrease in panel light transmittance, and the like. Aperture ratio, effect of reducing manufacturing cost
- Summary
- Abstract
- Description
- Claims
- Application Information
AI Technical Summary
Problems solved by technology
Method used
Image
Examples
Embodiment Construction
[0056] In order to make the above and other objects, features and advantages of the present invention more comprehensible, preferred embodiments are described below in detail with accompanying drawings.
[0057] Figure 1A , Figure 1B What is shown is a top view of the manufacturing process of the color filter layer according to an embodiment of the present invention.
[0058] First, please refer to Figure 1A, providing an active component array substrate 100, such as a thin film transistor array substrate. In the active device array substrate 100, a plurality of scanning wires 102 and a plurality of data wires 104 on the substrate 100' form a plurality of pixel regions 106, and a shared wire 108 passes through the pixel region 106, and a pixel electrode 110 is located in the pixel region. In 106 , the thin film transistor 112 is located at the intersection of the scan wire 102 and the data wire 104 . In this embodiment, the opaque metal pattern can be formed by metal patt...
PUM
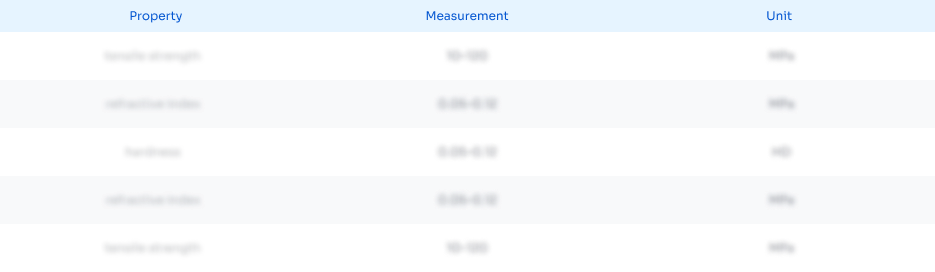
Abstract
Description
Claims
Application Information

- R&D
- Intellectual Property
- Life Sciences
- Materials
- Tech Scout
- Unparalleled Data Quality
- Higher Quality Content
- 60% Fewer Hallucinations
Browse by: Latest US Patents, China's latest patents, Technical Efficacy Thesaurus, Application Domain, Technology Topic, Popular Technical Reports.
© 2025 PatSnap. All rights reserved.Legal|Privacy policy|Modern Slavery Act Transparency Statement|Sitemap|About US| Contact US: help@patsnap.com