Rotary kiln
A rotary kiln and cylinder technology, applied in the field of rotary kiln, can solve the problems of high circumferential spacing of prefabricated blocks, inapplicability, large heat dissipation loss, etc., to reduce the probability of large-area damage to the furnace lining, strengthen the overall sealing performance, economical Benefit-enhancing effect
- Summary
- Abstract
- Description
- Claims
- Application Information
AI Technical Summary
Problems solved by technology
Method used
Image
Examples
Embodiment Construction
[0015] like figure 1 , 2 As shown, the rotary kiln of the present invention includes a cylinder body 1, a thermal insulation layer 2 and a furnace lining. The furnace lining is fixed on the cylinder body 1 by refractory bricks 3 through anchors 4, and the installation position on the refractory bricks 3 is in line with the axis of the rotary kiln cylinder body. There are hook holes 31 and hook concave surfaces 32 respectively on the two joint surfaces with the same direction (see image 3 ). see Figure 5 , 6 , 7, one end of the anchor 4 is provided with two hooks 41, which are respectively hooked into the hook holes 31 of the aforementioned two adjacent refractory bricks, and the other end of the anchor 4 is a welded body 42, which is welded on the cylinder 1, on a circle The interface of the inner refractory brick 3 is connected with castable 5 . Anchor nails 6 welded to the cylinder body 1 are arranged in the pouring material 5 .
[0016] like image 3 , 4 As shown,...
PUM
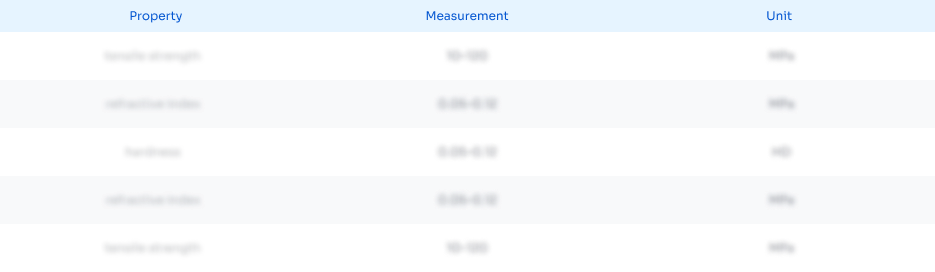
Abstract
Description
Claims
Application Information

- Generate Ideas
- Intellectual Property
- Life Sciences
- Materials
- Tech Scout
- Unparalleled Data Quality
- Higher Quality Content
- 60% Fewer Hallucinations
Browse by: Latest US Patents, China's latest patents, Technical Efficacy Thesaurus, Application Domain, Technology Topic, Popular Technical Reports.
© 2025 PatSnap. All rights reserved.Legal|Privacy policy|Modern Slavery Act Transparency Statement|Sitemap|About US| Contact US: help@patsnap.com