Brazing-sheet type heat exchanger capable of using three kinds of medium to exchange heat
A three-medium, brazing plate technology, used in heat exchanger types, indirect heat exchangers, heat exchange equipment, etc. Soldering or virtual welding and other problems, to ensure the effect of brazing quality and yield
- Summary
- Abstract
- Description
- Claims
- Application Information
AI Technical Summary
Problems solved by technology
Method used
Image
Examples
Embodiment Construction
[0038] figure 1 The shown brazed plate heat exchanger of the present invention capable of exchanging heat with three media has a baffle plate 13, a brazed sealing bevel 14 and six nozzles 7-12 and shows six corner hole channels 1-6. The first heat exchange medium is represented by the letter A, enters the corner hole channel 1 through the nozzle 7 and flows out from the corner hole channel 6 and the nozzle 12, and the second heat exchange medium is represented by the letter B, enters the corner hole through the nozzle 11 The hole channel 5 flows out from the corner hole channel 2 and the nozzle 8, and the third heat exchange medium is represented by the letter C, enters the corner hole channel 3 through the nozzle 9 and flows out from the corner hole channel 4 and the nozzle 10. The heat exchange medium B and the heat exchange medium A and C flow through the plate heat exchanger in a countercurrent manner, or flow through the plate heat exchanger in a smooth manner. At this ti...
PUM
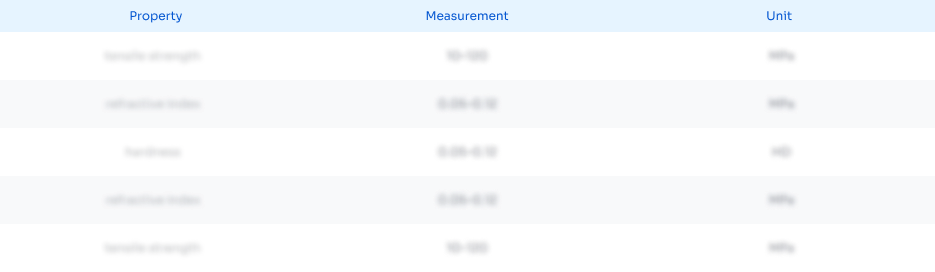
Abstract
Description
Claims
Application Information

- R&D
- Intellectual Property
- Life Sciences
- Materials
- Tech Scout
- Unparalleled Data Quality
- Higher Quality Content
- 60% Fewer Hallucinations
Browse by: Latest US Patents, China's latest patents, Technical Efficacy Thesaurus, Application Domain, Technology Topic, Popular Technical Reports.
© 2025 PatSnap. All rights reserved.Legal|Privacy policy|Modern Slavery Act Transparency Statement|Sitemap|About US| Contact US: help@patsnap.com