Catalyst composition and preparation method of fluorine silicon contained polymer
A silicon polymer and composition technology, applied in the field of catalyst composition, can solve problems such as low pass rate, fluctuating quality stability of fluorosilicon polymer, and poor uniformity
- Summary
- Abstract
- Description
- Claims
- Application Information
AI Technical Summary
Problems solved by technology
Method used
Image
Examples
preparation example Construction
[0026] The invention provides a method for preparing a fluorine-containing silicon polymer. The method of the present invention first selects the polymerization catalyst components. The ring-opening polymerization of organosilicon polymer generally uses anionic catalysts, that is, basic catalysts such as quaternary phosphorous bases, quaternary ammonium bases, alkali metal hydroxides and their Siliconate. The order of the strength of alkalinity is as follows: quaternary phosphorous alkali>quaternary ammonium alkali≥cesium hydroxide (CsOH)>potassium hydroxide (KOH)>sodium hydroxide (NaOH)>lithium hydroxide (LiOH). Generally speaking, the stronger the basicity, the lower the ring-opening polymerization temperature and the shorter the time to reach equilibrium. Literature reported D 3 F The anionic ring-opening polymerization process is as follows:
[0027]
[0028] From A to B is an irreversible process, B to C is a reversible process, when equilibrium is reached. 99% becomes oli...
Embodiment 1
[0075] 10kg D 3 F Monomer (purchased from Zhejiang Sanhuan Chemical Co., Ltd., purity>99.0%), 2g of methyl fluorosilicone oil (purchased from Shanghai Sanai Fluorine New Material Co., Ltd.) as molecular weight regulator and 50g D 4 MeVi Filter through 2# sand core funnel and add it into a pre-dried 20L stainless steel polymerization reactor. Add 40 g of the sodium siliconate catalyst component (polymerization degree about 55) prepared above into the catalyst dehydrator, leave about 500 g of monomer mixture on it, heat it with an infrared lamp, heat the kettle with steam, and control the temperature to 70± 3℃ / 1333.22~2666.44Pa, with dry N 2 Pre-dehydration for 1.5hr, and then the upper part D 3 FPut a small amount in the catalyst dehydrator, soak the alkali for dehydration for 0.5hr, put the catalyst components in the kettle within 15 minutes, wash with the monomers left on the upper part, put all the rinsed monomers into the kettle within 15 minutes, and mix Dehydrate for 0.5hr...
Embodiment 2
[0082] The steps described in Example 1 were repeated, except that the amount of the sodium siliconate catalyst component was 60 grams. The results are shown in Table 1. Six points were taken from different parts of the prepared polymer to compare the molecular weight distribution. The results are shown in Table 2.
PUM
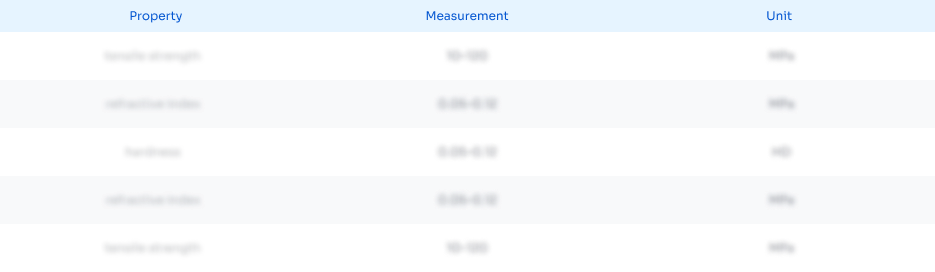
Abstract
Description
Claims
Application Information

- R&D
- Intellectual Property
- Life Sciences
- Materials
- Tech Scout
- Unparalleled Data Quality
- Higher Quality Content
- 60% Fewer Hallucinations
Browse by: Latest US Patents, China's latest patents, Technical Efficacy Thesaurus, Application Domain, Technology Topic, Popular Technical Reports.
© 2025 PatSnap. All rights reserved.Legal|Privacy policy|Modern Slavery Act Transparency Statement|Sitemap|About US| Contact US: help@patsnap.com