2,3-dichloropyridine synthesis method
A synthetic method and the technology of dichloropyridine, which are applied in two fields, can solve the problems of large consumption of auxiliary raw materials, high product cost, and large loss of solvent, so as to reduce the consumption of auxiliary raw materials, improve the working environment of the workshop, and suppress side effects. The effect of product formation
- Summary
- Abstract
- Description
- Claims
- Application Information
AI Technical Summary
Problems solved by technology
Method used
Examples
Embodiment 1
[0039] Add 23.5 g (0.25 mol) of 3-aminopyridine and 250 g industrial hydrochloric acid (≥31%) into a 1000 ml reaction flask, raise the temperature and stir to allow them to fully dissolve. Cool down to 4°C, control the liquid temperature in the range of 6-8°C, add 85g (0.25mol) of 10% hydrogen peroxide dropwise in 45 minutes, and continue the reaction at the same temperature for 1 hour. Use an ice-salt water bath to lower the material temperature to -5°C, start to drop 57.5g (0.25mol) of 30% sodium nitrite solution, control the material temperature -5°C to 0°C, take 20 minutes, and keep the temperature for 30 minutes. Then the temperature of the material is reduced to -5°C, and the catalyst solution composed of 3.75g of cuprous chloride dissolved in 47g of hydrochloric acid (≥31%) is added dropwise in 45 minutes, the temperature of the material is controlled at -5°C to -2°C, and the addition is completed Incubate and react at -2°C to 0°C for 1 hour. Change to a water bath and...
Embodiment 2
[0041] Add 23.5 g (0.25 mol) of 3-aminopyridine and 235 g industrial hydrochloric acid (≥31%) into the 1000 ml reaction flask, raise the temperature and stir to allow them to fully dissolve. Cool down to 5°C, control the liquid temperature in the range of 6-8°C, add 56.7g (0.25mol) of 15% hydrogen peroxide dropwise in 40 minutes, and continue the reaction at the same temperature for 2 hours. Use an ice-salt water bath to lower the material temperature to -2°C, start to drop 57.5g (0.25mol) of 30% sodium nitrite solution, control the material temperature -2°C to 0°C, take 25 minutes, and keep the temperature for 1 hour. Then the temperature of the material is reduced to -5°C, and the catalyst solution composed of 3.75g of cuprous chloride dissolved in 47g of hydrochloric acid (≥31%) is added dropwise in 55 minutes, and the temperature of the material is controlled at -5°C to 0°C. -2 ℃ ~ 0 ℃ heat preservation reaction for 30 minutes. Change to a water bath and allow the materia...
Embodiment 3
[0043] Add 23.5Kg (0.25kmol) of 3-aminopyridine and 250Kg industrial hydrochloric acid (≥31%) into the 300L reactor, stir and heat up to 30°C, and the materials are fully dissolved. The temperature was lowered to 4°C, and 85Kg (0.25Kmol) of 10% hydrogen peroxide was added dropwise within the range of 6-8°C for 55 minutes. The reaction was continued at the same temperature for 1 hour. Use ice brine instead to lower the material temperature to -5°C, start to drop 57.5Kg (0.25Kmol) of 30% sodium nitrite solution, control the material temperature -5~0°C, take 35 minutes, and react at the same temperature for 30 minutes. Lower the temperature of the material to -5°C, slowly add dropwise a mixture of 3.75Kg of cuprous chloride dissolved in 47Kg of hydrochloric acid (≥31%), and control the temperature of the material at -5°C to -3°C for 70 minutes After the addition, keep the reaction at -3°C to 0°C for 1 hour. The jacket was changed to river water, and the material was returned to...
PUM
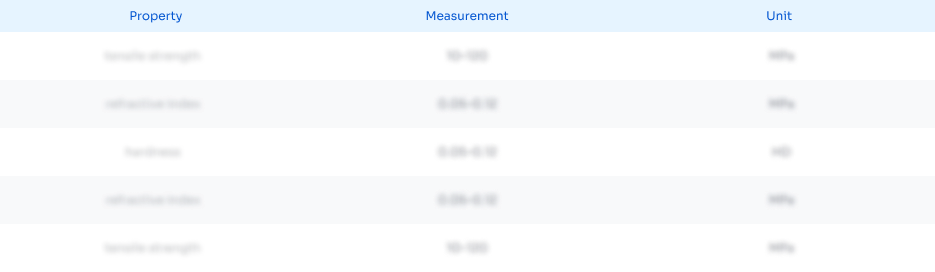
Abstract
Description
Claims
Application Information

- R&D
- Intellectual Property
- Life Sciences
- Materials
- Tech Scout
- Unparalleled Data Quality
- Higher Quality Content
- 60% Fewer Hallucinations
Browse by: Latest US Patents, China's latest patents, Technical Efficacy Thesaurus, Application Domain, Technology Topic, Popular Technical Reports.
© 2025 PatSnap. All rights reserved.Legal|Privacy policy|Modern Slavery Act Transparency Statement|Sitemap|About US| Contact US: help@patsnap.com