Variable temperature seat climate control system
a seat and variable temperature technology, applied in the field of variable temperature seats, can solve the problems of less effective use of temperature conditioned air in the cabin of the vehicle to heat or cool the occupant, maximize power efficiency, and seat known in the art that provides temperature conditioned air to the occupant do not operate in an electrically efficient manner, so as to minimize the possible discomfort of the occupan
- Summary
- Abstract
- Description
- Claims
- Application Information
AI Technical Summary
Benefits of technology
Problems solved by technology
Method used
Image
Examples
first embodiment
The first embodiment comprises conditioned air temperature sensors 102 and 104 positioned in the air flow of the temperature conditioned air passing to the seat, back and seat bottom, respectively, as shown in FIG. 2. The conditioned air temperature sensors are electrically connected to the controller 64. The temperature climate control algorithm described above and illustrated in FIG. 3 is configured to deactivate the Peltier modules in the event that the temperature of the conditioned air is greater than about 325.degree. K. or below about 297.degree. K. While the Peltier modules are deactivated the main exchanger fans continue to run.
FIG. 4 shows a second embodiment of the TCCS according to the practice of the present invention. The second embodiment is similar to the first embodiment in all respects, except for the addition of at least one ambient air temperature sensor 102 to monitor the temperature of the air outside of the VTS surrounding the occupant. The temperature sensor ...
second embodiment
The second embodiment also comprises conditioned air temperature sensors 128 and 130 positioned in the air flow of the temperature conditioned air passing to the seat, back and bottom, respectively, as shown in FIG. 4. The conditioned air temperature sensors are electrically connected to the controller 64. The temperature climate control algorithm described above and illustrated in FIG. 5 is configured to deactivate the Peltier modules in the event that the temperature of the conditioned air directed to the occupant is greater than about 325.degree. K. or below about 297.degree. K. While the Peltier modules are deactivated the main exchanger fans continue to run.
FIG. 6 shows a third embodiment of the TCCS according to the practice of this invention. The third embodiment is similar to the first embodiment in all respects except for two. One is the addition of at least one ambient air temperature sensor 132 to monitor the temperature of the air outside of the VTS surrounding the occup...
third embodiment
the TCCS as specifically described above and illustrated in FIG. 6 is used for controlling multiple VTSs in multi-occupant applications such as buses, trains, planes and the like. In such an application the main exchanger fan, waste exchanger fan, Peltier modules, temperature sensor, and weight sensitive switch from each VTS are electrically connected to a common controller. Multiple ambient air temperature sensors may be placed at different locations within the vehicle to provide an accurate temperature profile throughout the interior of the vehicle. The common controller is configured to accommodate inputs from the multiple ambient air temperature sensors. The common controller may be configured to control the main fan speed and mode of operation for the Peltier modules in the same manner as that specifically described above and illustrated in FIG. 7, taking into account the possibility of different ambient temperature zones within the vehicle surrounding each VTS.
Although limited...
PUM
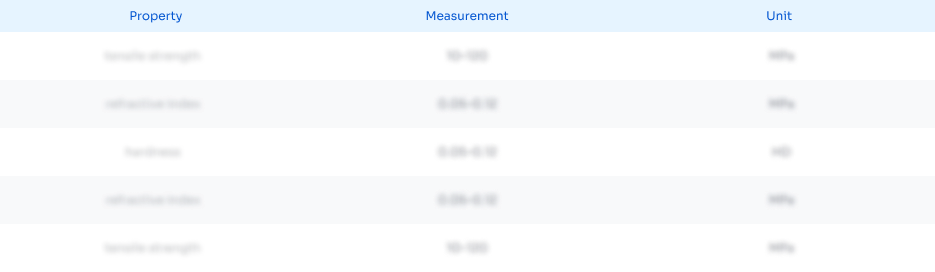
Abstract
Description
Claims
Application Information

- R&D
- Intellectual Property
- Life Sciences
- Materials
- Tech Scout
- Unparalleled Data Quality
- Higher Quality Content
- 60% Fewer Hallucinations
Browse by: Latest US Patents, China's latest patents, Technical Efficacy Thesaurus, Application Domain, Technology Topic, Popular Technical Reports.
© 2025 PatSnap. All rights reserved.Legal|Privacy policy|Modern Slavery Act Transparency Statement|Sitemap|About US| Contact US: help@patsnap.com