De-icing arrangement and method for de-icing a structural element
a structural element and arrangement technology, applied in the direction of de-icing equipment, aircraft components, transportation and packaging, etc., can solve the problems of ice accretion on aircrafts, serious perturbations of flying conditions, and threatening events, and achieve the effect of improving the de-icing of structural elements
- Summary
- Abstract
- Description
- Claims
- Application Information
AI Technical Summary
Benefits of technology
Problems solved by technology
Method used
Image
Examples
Embodiment Construction
[0043]A de-icing arrangement for de-icing a structural element comprises at least one actuator for removing ice from the structural element, a capacitive storage bank and a control unit arranged to control discharge of the capacitive storage bank to provide an excitation pulse to the at least one electromagnetic actuator so as to force the actuator to apply a mechanical force on the structural element so as to provide a chock in the structural element. This may result in removal of ice from the structural element. The actuator is arranged to expand in at least one direction when fed with the excitation pulse. The actuator is arranged in relation to the structural element so that mechanical force caused by the expansion on the structural element will be applied to the structure element.
[0044]The capacitive storage bank comprises a plurality of selectable capacitors of different capacitance. The control unit is arranged to select at least one capacitor for charging having a total capa...
PUM
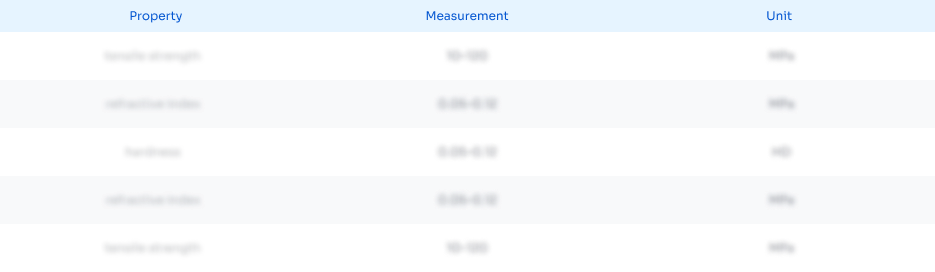
Abstract
Description
Claims
Application Information

- R&D
- Intellectual Property
- Life Sciences
- Materials
- Tech Scout
- Unparalleled Data Quality
- Higher Quality Content
- 60% Fewer Hallucinations
Browse by: Latest US Patents, China's latest patents, Technical Efficacy Thesaurus, Application Domain, Technology Topic, Popular Technical Reports.
© 2025 PatSnap. All rights reserved.Legal|Privacy policy|Modern Slavery Act Transparency Statement|Sitemap|About US| Contact US: help@patsnap.com