Practical steam engine
a steam engine and steam technology, applied in the direction of machines/engines, oscillatory slide valves, mechanical equipment, etc., can solve the problems of low density, low heating value solids, liquids and gaseous substances, and low cost of high-grade commercial fuels, and achieve low torque output, high speed, and add value to the process of wood products
- Summary
- Abstract
- Description
- Claims
- Application Information
AI Technical Summary
Benefits of technology
Problems solved by technology
Method used
Image
Examples
Embodiment Construction
[0031]The present invention is described more fully hereinafter with reference to the accompanying drawings, in which preferred embodiments of the invention are shown. This invention may, however, may be embodied in many different forms and should not be construed as limited to the embodiments set for herein; rather, these embodiments are provided so that this disclosure will be thorough and complete and will fully convey the scope of the invention to those skilled in the art. The current invention is a high speed, two-stroke engine that is counter flow, semi-uniflow, or uniflow and is comprised of at least one variable rotary valve mechanism. Working fluid, referred to herein, may be organic and / or inorganic fluid, naturally occurring and / or man-made. Working fluid may include: Chlorofluorocarbon (CFC) (e.g. R-11, R-12); Hydro-fluorocarbons (HFC) (e.g. R-134a, R-245fa); Hydro-chlorofluorocarbon (HCFC) (e.g. R-22, R-123); Hydrocarbons (HC) (e.g. Butane, methane, pentane, propane, et...
PUM
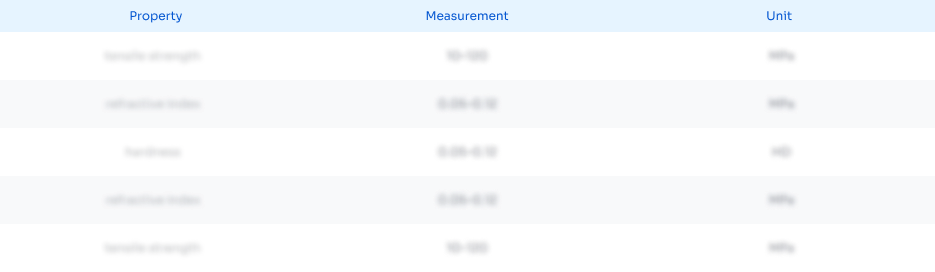
Abstract
Description
Claims
Application Information

- R&D
- Intellectual Property
- Life Sciences
- Materials
- Tech Scout
- Unparalleled Data Quality
- Higher Quality Content
- 60% Fewer Hallucinations
Browse by: Latest US Patents, China's latest patents, Technical Efficacy Thesaurus, Application Domain, Technology Topic, Popular Technical Reports.
© 2025 PatSnap. All rights reserved.Legal|Privacy policy|Modern Slavery Act Transparency Statement|Sitemap|About US| Contact US: help@patsnap.com