Direct use of acoustic power in stirling engine for heat removal
- Summary
- Abstract
- Description
- Claims
- Application Information
AI Technical Summary
Benefits of technology
Problems solved by technology
Method used
Image
Examples
Embodiment Construction
[0014]Reference is now made to FIG. 2, which illustrates a block diagram of Stirling engine 10, constructed and operative in accordance with a non-limiting embodiment of the present invention.
[0015]As in a typical Stirling engine, the Stirling engine 10 has a piston 12 and a displacer 14 that move in phased reciprocating motion within cylinders 16 which, in some embodiments of the Stirling engine, may be a single cylinder. A working fluid 15 contained within cylinders 16 is constrained by seals from escaping around piston 12 and displacer 14. The working fluid 15 is chosen for its thermodynamic properties, e.g., helium at a pressure of several atmospheres. The position of displacer 14 governs whether working fluid 15 is in contact with a hot interface (or hot heat exchanger) 18 or a cold interface (or cold heat exchanger) 20, corresponding respectively to the interfaces at which heat is supplied to and extracted from working fluid 15. The volume of working fluid 15 governed by the p...
PUM
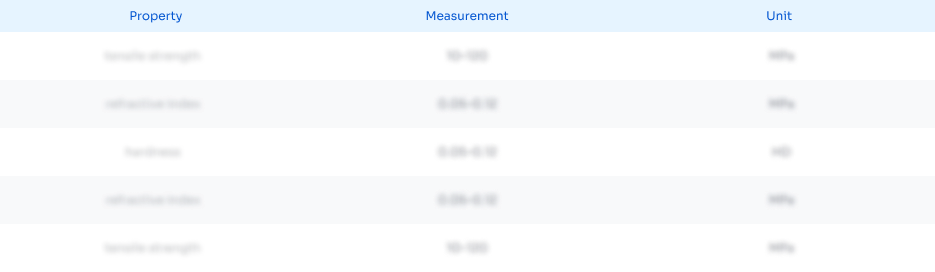
Abstract
Description
Claims
Application Information

- R&D
- Intellectual Property
- Life Sciences
- Materials
- Tech Scout
- Unparalleled Data Quality
- Higher Quality Content
- 60% Fewer Hallucinations
Browse by: Latest US Patents, China's latest patents, Technical Efficacy Thesaurus, Application Domain, Technology Topic, Popular Technical Reports.
© 2025 PatSnap. All rights reserved.Legal|Privacy policy|Modern Slavery Act Transparency Statement|Sitemap|About US| Contact US: help@patsnap.com