Injection valve for internal combustion engines
a technology for injection valves and internal combustion engines, which is applied in the direction of machines/engines, liquid fuel feeders, mechanical apparatuses, etc., can solve the problems of increasing soot emissions, and achieve the effect of positively modifying the pressure conditions in the hole outlet section and increasing the soot emission in the exhaust gas
- Summary
- Abstract
- Description
- Claims
- Application Information
AI Technical Summary
Benefits of technology
Problems solved by technology
Method used
Image
Examples
Embodiment Construction
[0011]The injection valve of which a part is shown schematically in FIG. 1, with its injecting end shown in longitudinal section, for injecting fuel into a combustion cylinder of an internal combustion engine has a sleeve-type valve seat bearer 11 that extends from a valve housing (not shown here) and is terminated at its free end by a valve seat element 12. On the inner wall, limiting a valve chamber 13, of valve seat element 12 there is fashioned a valve seat 14 in the form of an annular surface that is concentric to the axis of valve seat element 12, and that, together with a closing head 15 of a valve member 16 situated so as to be axially displaceable in valve seat bearer 12, forms a so-called sealing seat. Closing head 15 is fastened, e.g. welded, to the frontal end of a hollow cylindrical valve needle 17 of valve member 16. Valve needle 17 has radial bores 18 and is connected to a fuel supply line (not shown here) that is fashioned in the valve housing, so that fuel moves fro...
PUM
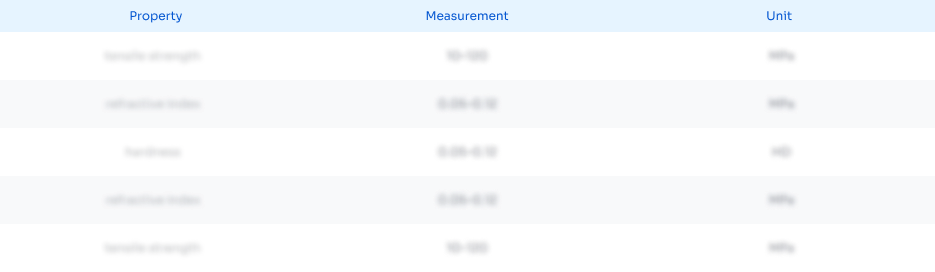
Abstract
Description
Claims
Application Information

- R&D
- Intellectual Property
- Life Sciences
- Materials
- Tech Scout
- Unparalleled Data Quality
- Higher Quality Content
- 60% Fewer Hallucinations
Browse by: Latest US Patents, China's latest patents, Technical Efficacy Thesaurus, Application Domain, Technology Topic, Popular Technical Reports.
© 2025 PatSnap. All rights reserved.Legal|Privacy policy|Modern Slavery Act Transparency Statement|Sitemap|About US| Contact US: help@patsnap.com