Slat monitoring system
- Summary
- Abstract
- Description
- Claims
- Application Information
AI Technical Summary
Benefits of technology
Problems solved by technology
Method used
Image
Examples
Embodiment Construction
[0037]Referring first to FIG. 2, there is shown a simplified plan view of the inside of an aircraft wing 10 having a plurality of slats 11 along its leading edge 12. A common input drive shaft 13 extends along the length of the wing 10 just inside its leading edge 12 and a rotary actuator 14 is positioned at spaced locations along the length of the common input drive shaft 13. Although the common input drive shaft 13 may be fabricated in sections, those sections are coupled together so that the entire input drive shaft 13 rotates as one in response to rotation of a slat deployment motor 15 located at the inboard end of the wing 1. Two sections of the common input drive shaft 4 may be coupled by a gearbox 16 to accommodate changes in the angle of the wing leading edge 12, which is mirrored by the common input drive shaft 13. Gearbox 16 therefore couples the sections together so that each section may not share the same axis of rotation.
[0038]A wingtip brake 17 may be mounted on the ou...
PUM
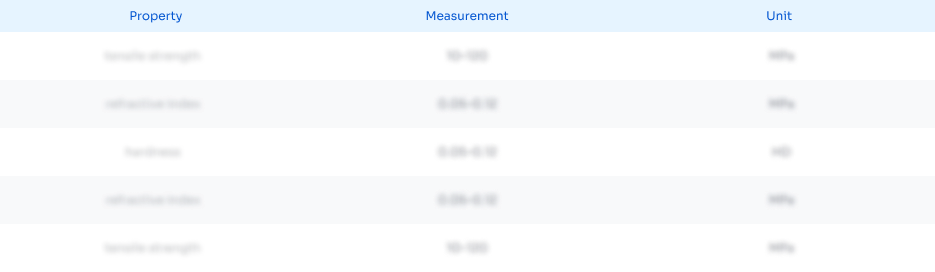
Abstract
Description
Claims
Application Information

- R&D
- Intellectual Property
- Life Sciences
- Materials
- Tech Scout
- Unparalleled Data Quality
- Higher Quality Content
- 60% Fewer Hallucinations
Browse by: Latest US Patents, China's latest patents, Technical Efficacy Thesaurus, Application Domain, Technology Topic, Popular Technical Reports.
© 2025 PatSnap. All rights reserved.Legal|Privacy policy|Modern Slavery Act Transparency Statement|Sitemap|About US| Contact US: help@patsnap.com