Folded cardboard concrete form system
a concrete form system and cardboard technology, applied in the field of form systems, can solve the problems of labor costs, labor costs, and increased labor costs of building materials, and achieve the effect of quick and easy erection
- Summary
- Abstract
- Description
- Claims
- Application Information
AI Technical Summary
Benefits of technology
Problems solved by technology
Method used
Image
Examples
Embodiment Construction
[0030]Referring to the figures in detail and first to FIG. 1A, there is shown an exemplary embodiment of a first sheet (hereinafter, also referred to as “base sheet”) of cardboard 10 used in the form system of the present invention. In one embodiment, the base sheet 10 comprises double thick cardboard. In other embodiments, the base sheet 10 can comprise cardboard having other thicknesses (e.g., single thick, triple thick). FIG. 1A shows the base sheet 10 having a plurality of folding sections 11, 12 defined by creases or pre-scored lines extending the length of the base sheet. The folding sections 11, 12 provide for the base sheet 10 to be corrugated into a first shape. More specifically, folding sections 12 with its pre-scored lines are adapted to allow for the base sheet 10 to be folded in one direction (e.g. upward direction) while the folding sections 11 with its pre-scored lines are adapted to allow for the base sheet 10 to be folded in an opposite direction (e.g. downward dir...
PUM
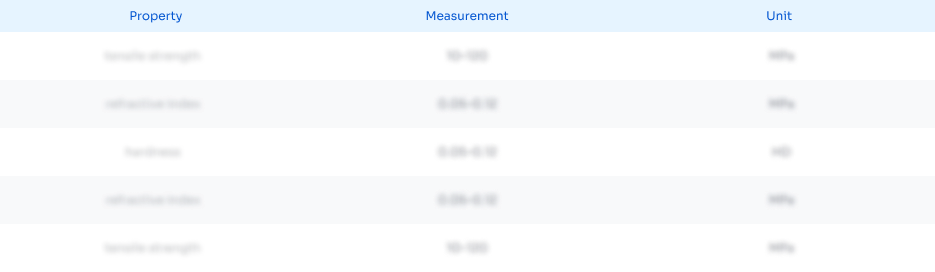
Abstract
Description
Claims
Application Information

- R&D
- Intellectual Property
- Life Sciences
- Materials
- Tech Scout
- Unparalleled Data Quality
- Higher Quality Content
- 60% Fewer Hallucinations
Browse by: Latest US Patents, China's latest patents, Technical Efficacy Thesaurus, Application Domain, Technology Topic, Popular Technical Reports.
© 2025 PatSnap. All rights reserved.Legal|Privacy policy|Modern Slavery Act Transparency Statement|Sitemap|About US| Contact US: help@patsnap.com