Base Mat Assembly And Method For Constructing The Same
a technology of lng tanks and base mats, which is applied in the direction of girders, joists, building repairs, etc., can solve the problems of difficult design and construction of such connections, and the application of prefabricated elements in lng tank foundations is not a conventional approach
- Summary
- Abstract
- Description
- Claims
- Application Information
AI Technical Summary
Benefits of technology
Problems solved by technology
Method used
Image
Examples
Embodiment Construction
I. Overview
[0035]In a first embodiment, a full containment LNG tank 18 is shown in FIGS. 1 and 2. The LNG tank 18 comprises an outer secondary container, hereinafter “outer tank 20” surrounding an inner primary container, hereinafter “inner tank 22”. Inner tank 22 is intended to store LNG. Outer tank 20 is preferably a full containment tank in which both LNG and gas vapor are fully contained in the event of a leak from the inner tank 22.
[0036]In this particular embodiment, outer tank 20 is primarily made of precast reinforced concrete elements which reduce fire risk relative to using a primarily steel outer container or tank. The construction of outer tank 20 involves assembling precast reinforced concrete elements for a foundation 24, including a base mat assembly 100 and an outer ring beam 200, an outer wall or shell 300 and a roof 400. As an example of order of magnitude, outer tank 20 in this embodiment has a diameter of approximately 80 meters, an overall height (to the top of ...
PUM
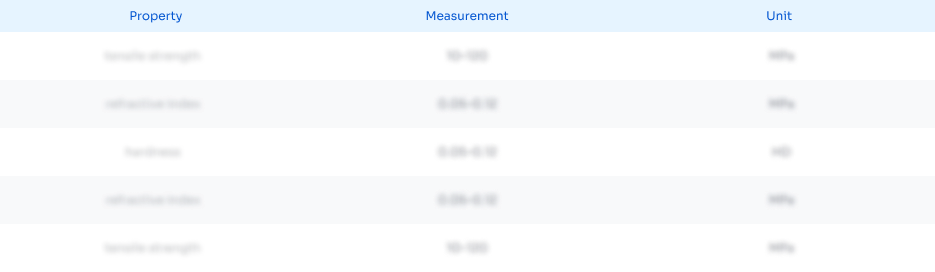
Abstract
Description
Claims
Application Information

- R&D
- Intellectual Property
- Life Sciences
- Materials
- Tech Scout
- Unparalleled Data Quality
- Higher Quality Content
- 60% Fewer Hallucinations
Browse by: Latest US Patents, China's latest patents, Technical Efficacy Thesaurus, Application Domain, Technology Topic, Popular Technical Reports.
© 2025 PatSnap. All rights reserved.Legal|Privacy policy|Modern Slavery Act Transparency Statement|Sitemap|About US| Contact US: help@patsnap.com