Bearing Wheels
a technology of bearing wheels and bearings, which is applied in the direction of skateboards, roller skates, sports apparatus, etc., can solve the problems of poor wheel performance and damage, loss of grease from bearings, and inconvenient tolerance across bearing diameters of conventional bearing wheels to promote longer life of bearings, so as to improve the resistance to heat conduction and expansion of the wheel centre, improve the air flow, and improve the effect of heat dissipation
- Summary
- Abstract
- Description
- Claims
- Application Information
AI Technical Summary
Benefits of technology
Problems solved by technology
Method used
Image
Examples
first embodiment
[0054]With reference now to a bearing wheel according to the invention shown in FIGS. 1 to 4, the bearing wheel 10 includes a wheel centre 12, a pair of bearings 14, 16 housed in the wheel centre and adapted to allow the wheel centre to spin about an axle 18 around which the bearings are mounted. The bearing wheel 10 also includes an outer surface 20 for contacting a frictional surface, such as the ground, over which the wheel centre is to roll. There are also air flow passageways 22 formed through the wheel centre. The air flow passageways extend between opposite sides of the wheel centre to allow air flow therethrough to dissipate excess heat caused by friction while the wheel is moving on the frictional surface.
[0055]The wheel centre 12 has a main body portion 24 that is offset to one side of the wheel 10 so that one side 26 of the main body portion is substantially in the plane of one side of the outer surface and the other side 27 of the main body portion is recessed from the p...
second embodiment
[0065]With reference now to a bearing wheel according to the invention shown in FIGS. 5 to 8, the bearing wheel 50 is similar to the bearing wheel 10 except in the way that the cap is secured upon the outer portion of the wheel centre. For ease of reference, like features have been given like numerals. Reference should be made to the above description of the bearing wheel 10 for an understanding of the structure and function of the like features in the bearing wheel 50.
[0066]The outer portion 52 of the wheel centre 53 has a projecting annular rib 54 surrounded on both sides by circumferential grooves 56, 58. The rib 54 has a plurality of equally spaced apart holes 60 drilled across it. The surface profile of the outer portion 52 allows the cap 62 to be secured upon it in an improved way. When, say, molten polyurethane is poured into the mould that forms the cap upon the wheel centre during manufacture, the polyurethane flows into the grooves 56, 58 and through the holes 60 to form a...
third embodiment
[0067]With reference now to a bearing wheel according to the invention shown in FIGS. 9 to 12, the bearing wheel 70 is similar to the bearing wheels 10 and 50 except that it lacks a stepped recess in one side of the wheel centre, and in the way that the cap is secured upon the outer portion of the wheel centre. For ease of reference, like features have been given like numerals. Reference should be made to the above description of the bearing wheels 10 and 50 for an understanding of the structure and function of the like features in the bearing wheel 70.
[0068]The bearing wheel 70 is manufactured to be of smaller width and diameter than the bearing wheels 10 and 50. The bearing wheel 70 lacks a stepped recess in one side of the wheel centre 72. The wheel centre 72 has a main body portion 74 that is symmetrical, and both sides of the main body portion 74 are outermost and present a respective face at which there are openings 76 to respective passageways 77.
[0069]Despite the absence of ...
PUM
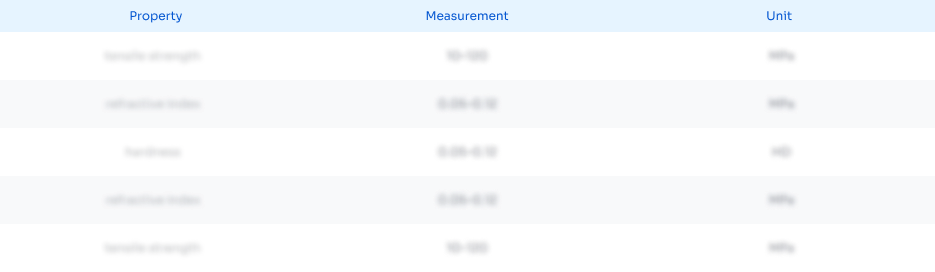
Abstract
Description
Claims
Application Information

- R&D
- Intellectual Property
- Life Sciences
- Materials
- Tech Scout
- Unparalleled Data Quality
- Higher Quality Content
- 60% Fewer Hallucinations
Browse by: Latest US Patents, China's latest patents, Technical Efficacy Thesaurus, Application Domain, Technology Topic, Popular Technical Reports.
© 2025 PatSnap. All rights reserved.Legal|Privacy policy|Modern Slavery Act Transparency Statement|Sitemap|About US| Contact US: help@patsnap.com