Screw compressor
- Summary
- Abstract
- Description
- Claims
- Application Information
AI Technical Summary
Benefits of technology
Problems solved by technology
Method used
Image
Examples
first embodiment
[0029]FIG. 1 shows a first embodiment according to the invention. In the following description, although a twin screw compressor having two male and female screw rotors are exemplified as the embodiment, the invention is not limited to the twin screw compressor, but may be also applied to a single screw compressor having one screw rotor.
[0030]As shown in FIG. 1, a screw compressor includes a motor casing 1, a main casing 2, and a discharge casing 3 which are connected to each other. The motor casing 1 accommodates a driving motor 4 which drives a compression mechanism portion, and is fixed to the main casing 2 through means such as bolts. The main casing 2 is provided with a cylindrical bore 5 and a suction port 6 which introduces a refrigerant gas into the cylindrical bore 5. The cylindrical bore 5 accommodates a female rotor (not shown) and a male rotor 14, rotatably supported by roller bearings 7, 8, and 9 (the low-pressure-side bearings 7 and 8 and the high-pressure-side bearing...
second embodiment
[0045]FIG. 2 shows a second embodiment according to the invention. As in the embodiment of FIG. 1, the steel pipe chamber includes the low-pressure-side chamber 21 and the high-pressure-side chambers 22 and 23. Since the flanges 24, 25, 26, and 27 formed in the chambers are connected to each other through means such as bolts, the low-pressure-side chamber 21 and the high-pressure-side chambers 22 and 23 are sealed from each other, are sealed from the ambient air, and are able to be divided.
[0046]The embodiment is different from the first embodiment in that the flange 29 formed in the motor casing 1 and the flange 28 formed inside the high-pressure-side chamber 22 are connected to each other through bolts with the sealing component 30 interposed therebetween. Even in the embodiment, the spaces 31 and 32 inside the steel pipe chamber are divided into the space 31 as the low-pressure-side space and the space 32 as the high-pressure-side space. Additionally, it is possible to cool the d...
third embodiment
[0047]FIG. 3 shows a third embodiment according to the invention. As in the embodiment of FIG. 1, the steel pipe chamber includes the low-pressure-side chamber 21 and the high-pressure-side chamber 22. In addition, the flanges 24 and 25 formed in the chambers are connected to each other through means such as bolts so as to be sealed from each other, and are able to be divided. In the embodiment, the flange 29 formed in the main casing 2 and the flange 28 formed in the inside of the low-pressure-side chamber 21 are connected to each other through bolts with the sealing component 30 interposed therebetween. The spaces 31 and 32 inside the steel pipe chamber is divided into the space 31 as the low-pressure-side space and the space 32 as the high-pressure-side space. Even in the embodiment, it is possible to cool the driving motor 4 by using the low-pressure and low-temperature refrigerant gas, and to dispose the oil separator in the inside of the steel pipe chamber. Further, it is poss...
PUM
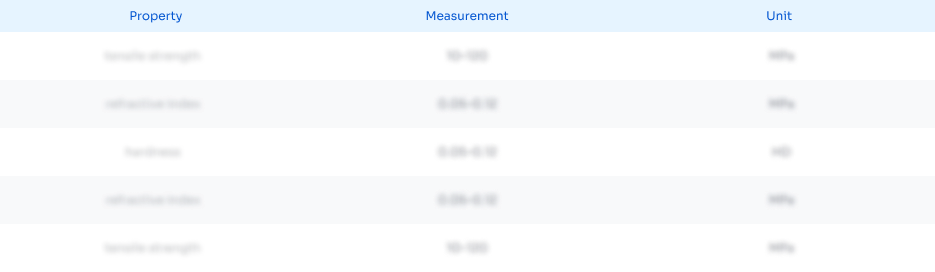
Abstract
Description
Claims
Application Information

- R&D
- Intellectual Property
- Life Sciences
- Materials
- Tech Scout
- Unparalleled Data Quality
- Higher Quality Content
- 60% Fewer Hallucinations
Browse by: Latest US Patents, China's latest patents, Technical Efficacy Thesaurus, Application Domain, Technology Topic, Popular Technical Reports.
© 2025 PatSnap. All rights reserved.Legal|Privacy policy|Modern Slavery Act Transparency Statement|Sitemap|About US| Contact US: help@patsnap.com