Assembly for an aircraft including a wing element and a suspension pylon
a technology of suspension pylons and aircraft, which is applied in the direction of aircraft power plants, power plant construction, power plant types, etc., can solve the problems of increasing restrictions in the space between the wing, the suspension pylons and the different attachments, and the overall dimension is extremely large, so as to achieve the effect of improving adaptability and further increasing ground clearan
- Summary
- Abstract
- Description
- Claims
- Application Information
AI Technical Summary
Benefits of technology
Problems solved by technology
Method used
Image
Examples
first embodiment
[0042]However, in the configuration shown for this first embodiment and as can be seen in FIGS. 2 and 3, the only fastening means provided between the closing element 28 and the forward spar 34 are a plurality of tension bolts 38, and two lateral shear pins 40. More precisely, these mounting means 8 preferably have a symmetry about a vertical plane parallel to a direction 42 orthogonal to the width direction 32 and therefore comprise two shear pins 40 arranged on each side of this plane (not shown), these pins 40 also being arranged along this direction 42 and therefore each of them being capable of resisting forces applied along a first and a second directions orthogonal to each other and also orthogonal to the direction 42. Note also that the above-mentioned vertical plane also preferably forms a plane of symmetry for the closing element 28.
[0043]The mounting means 8 also comprise tension bolts 38 also arranged in the direction 42 along which a plurality of force loading ribs 44 o...
second embodiment
[0047]Therefore, in this second embodiment and in the other described embodiments, the entire rigid structure 6 of the pylon 4 is preferably forwards from the forward spar 34 of the wing 2.
[0048]With reference to FIG. 5, the figure shows an assembly 1 for an aircraft according to a third preferred embodiment of this invention. In this mode, there is a support fitting 152 preferably provided with reinforcing ribs 153, and for which the lower part located outside the wing 2 is identical to or similar to the support fitting 52 described in the context of the second embodiment, and an upper part located outside the wing 2 is inserted between the forward spar 34 and the closing element 28. Thus, this final element 28 that is still bearing in contact with the spar 34 without being directly in contact with it, is consequently entirely in contact with a bearing surface 154 of the fitting 152, this surface 154 and the element 28 then being partially inside and partially outside the wing 2.
[0...
PUM
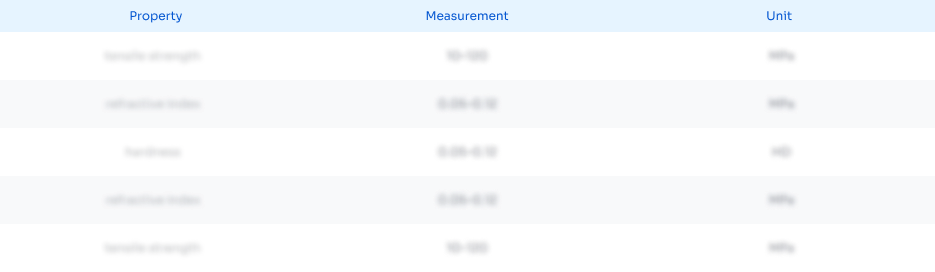
Abstract
Description
Claims
Application Information

- R&D
- Intellectual Property
- Life Sciences
- Materials
- Tech Scout
- Unparalleled Data Quality
- Higher Quality Content
- 60% Fewer Hallucinations
Browse by: Latest US Patents, China's latest patents, Technical Efficacy Thesaurus, Application Domain, Technology Topic, Popular Technical Reports.
© 2025 PatSnap. All rights reserved.Legal|Privacy policy|Modern Slavery Act Transparency Statement|Sitemap|About US| Contact US: help@patsnap.com