Roll-forming machine for forming smooth curves in profiled panel sections and method of forming curved panels
- Summary
- Abstract
- Description
- Claims
- Application Information
AI Technical Summary
Benefits of technology
Problems solved by technology
Method used
Image
Examples
Embodiment Construction
[0024]A panel curving apparatus for roll forming smooth longitudinal curves in profiled panel sections according to the present invention is shown generally as 10 in FIG. 1. The preferred curving apparatus 10 includes three main sections, namely a first tooling raft 12, a central instrumentation and control station 14 and a second tooling raft 16. As will be explained in more detail below the first and second tooling rafts 12, 16 are generally similar in operation, but may be provided with different roller tooling configurations to facilitate the use of the invention. For example, in one preferred embodiment the first tooling raft 12 can have rollers 15 that are suitable for N-Decking type panel material and the second tooling raft can have rollers 17 that are suitable for a liner panel for the N-Decking panels of the first tooling raft. It will be noted from FIG. 1 that the rollers are oriented on a generally vertical axis of rotation for example as shown at A for reasons explained...
PUM
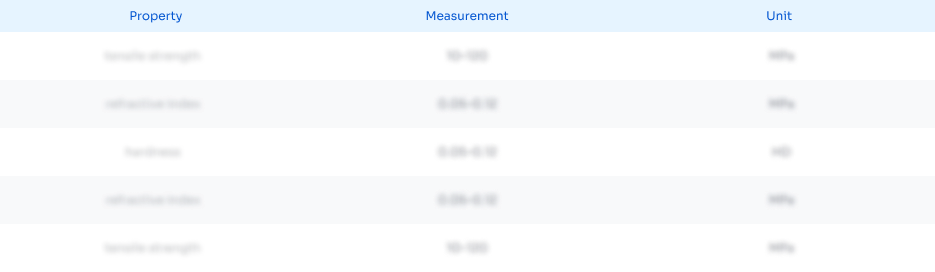
Abstract
Description
Claims
Application Information

- R&D
- Intellectual Property
- Life Sciences
- Materials
- Tech Scout
- Unparalleled Data Quality
- Higher Quality Content
- 60% Fewer Hallucinations
Browse by: Latest US Patents, China's latest patents, Technical Efficacy Thesaurus, Application Domain, Technology Topic, Popular Technical Reports.
© 2025 PatSnap. All rights reserved.Legal|Privacy policy|Modern Slavery Act Transparency Statement|Sitemap|About US| Contact US: help@patsnap.com