Method of repairing a fuel nozzle
- Summary
- Abstract
- Description
- Claims
- Application Information
AI Technical Summary
Problems solved by technology
Method used
Image
Examples
Embodiment Construction
[0031]A gas turbine engine has a combustion chamber housed within an engine outer casing. Fuel is supplied into the combustion chamber by fuel nozzles, such as for example shown in FIGS. 1 and 2. Liquid fuel is transported through conduits 80 within a stem 83, such as, for example, shown in FIG. 1, to the fuel nozzle tip assembly 68. Conduits that have a unitary construction may be used for transporting the liquid fuel into the fuel nozzle tip assembly 68 of the fuel nozzles. The fuel supply conduits, may be located within the stem 83 and coupled to a fuel distributor tip 180. Pilot fuel and main fuel are sprayed into the combustor by fuel nozzle tip assemblies 68, such as for example, shown in FIGS. 1 and 2. During operation of the turbine engine, initially, pilot fuel is supplied through a pilot fuel flow passage, such as, for example, shown as items 102, 104 in FIG. 2, during pre-determined engine operation conditions, such as during startup and idle operations. The pilot fuel is...
PUM
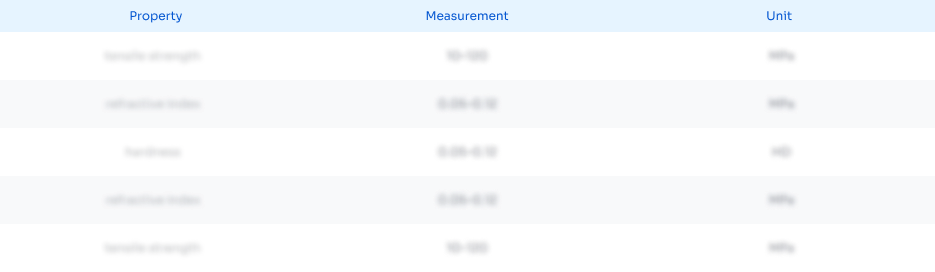
Abstract
Description
Claims
Application Information

- R&D
- Intellectual Property
- Life Sciences
- Materials
- Tech Scout
- Unparalleled Data Quality
- Higher Quality Content
- 60% Fewer Hallucinations
Browse by: Latest US Patents, China's latest patents, Technical Efficacy Thesaurus, Application Domain, Technology Topic, Popular Technical Reports.
© 2025 PatSnap. All rights reserved.Legal|Privacy policy|Modern Slavery Act Transparency Statement|Sitemap|About US| Contact US: help@patsnap.com