Quick change tool for die casting metal
a technology of die casting metal and tool, which is applied in the direction of manufacturing tools, metal-working apparatus, shaping tools, etc., can solve the problems of time-consuming process of precisely positioning the heavy die on the platen, significant per piece cost of die casting products, and the time-consuming die casting process
- Summary
- Abstract
- Description
- Claims
- Application Information
AI Technical Summary
Benefits of technology
Problems solved by technology
Method used
Image
Examples
Embodiment Construction
[0018]In accordance with the present invention, a quick change tool for casting metal is disclosed. The tool and method consists of components configured and correlated with respect to each other so as to attain the desired objective. FIG. 1 shows a quick change die assembly 100 mounted in a mold machine 200. The die assembly 100 mounts to the upper platen 200A and the lower platen 200B of a conventional die casting mold machine 200. Clamps 102 hold bolts 104 used to mount the die assembly 100 to the upper 200A and lower 200B platens. The clamps 102A hold an upper die shoe 110 to the upper platen 200A. The upper die shoe 110 includes a slot 112 to accommodate each clamp 102A. The lower die shoe 120 also includes a slot 122 around its perimeter to accommodate clamps 102B. The upper die shoe110 has upper die rails 130, 132, 134 and 136 bolted to it to form a plate like frame. The lower die shoe 120 has lower die rails 140, 142, 144 and 146 bolted to it to form a lower plate like frame...
PUM
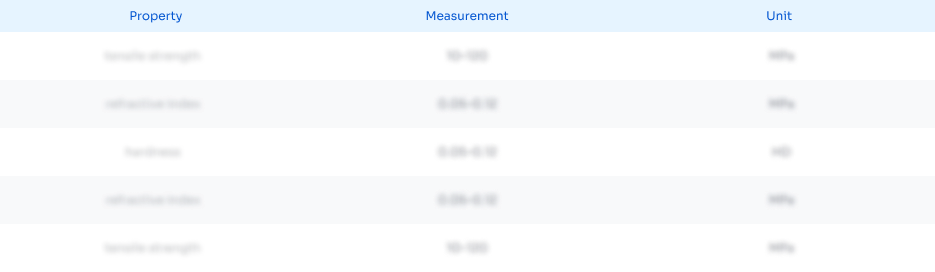
Abstract
Description
Claims
Application Information

- R&D Engineer
- R&D Manager
- IP Professional
- Industry Leading Data Capabilities
- Powerful AI technology
- Patent DNA Extraction
Browse by: Latest US Patents, China's latest patents, Technical Efficacy Thesaurus, Application Domain, Technology Topic, Popular Technical Reports.
© 2024 PatSnap. All rights reserved.Legal|Privacy policy|Modern Slavery Act Transparency Statement|Sitemap|About US| Contact US: help@patsnap.com