Method and apparatus for residue detection on a polished wafer
a technology of residue detection and polishing, applied in the direction of electrical equipment, material analysis, instruments, etc., can solve the problems of affecting the quality of the final product, not removing the entire metal layer, and leaving residue on the processed wafer
- Summary
- Abstract
- Description
- Claims
- Application Information
AI Technical Summary
Benefits of technology
Problems solved by technology
Method used
Image
Examples
Embodiment Construction
[0047]FIGS. 1a and 1b are schematic drawings of side (a) and front (b) projections of the present invention apparatus arrangement 2, mounted on a parent tool 4. The static FIG. 1a presentation corresponds to a certain moment in parent tool 4 robot dynamics, when a wafer 6 settles on download lifter 8 in its uppermost position, before descending to the output cassette 10. The electronic section 12 of the parent tool 4 then produces a trigger signal, which is fed through link 14 to the apparatus computer 16. The computer in turn triggers a camera 18 through link 20 after a necessary delay, when the utmost opening of robots arm's wafer grip 22 causes no line-of-sight obstruction from camera 18 to wafer 6. The inspection tool illumination source 24 and camera 18 are mounted on supporting structure 26, which is clamped to the chassis of the parent tool 4. The illumination source 24 and camera 18 are both inclined by about 30° angles α, β, respectively, relative to vertical (in opposite d...
PUM
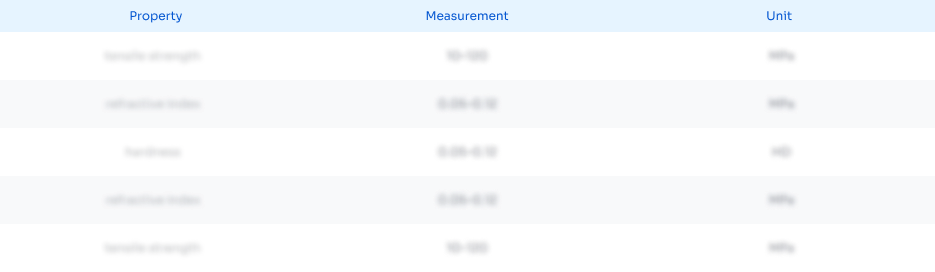
Abstract
Description
Claims
Application Information

- R&D
- Intellectual Property
- Life Sciences
- Materials
- Tech Scout
- Unparalleled Data Quality
- Higher Quality Content
- 60% Fewer Hallucinations
Browse by: Latest US Patents, China's latest patents, Technical Efficacy Thesaurus, Application Domain, Technology Topic, Popular Technical Reports.
© 2025 PatSnap. All rights reserved.Legal|Privacy policy|Modern Slavery Act Transparency Statement|Sitemap|About US| Contact US: help@patsnap.com