Two-step roller finger cam follower
a roller finger cam and follower technology, applied in the direction of valve details, valve springs, valve arrangements, etc., can solve the problems of increased force requirements of lost motion and valve springs, inconvenient operation, and inability to adjust the angle of the roller finger cam, etc., to achieve the effect of reducing the range of lost motion of the central slider, reducing the force requirements of the lost motion and the valve spring, and reducing the overall volum
- Summary
- Abstract
- Description
- Claims
- Application Information
AI Technical Summary
Benefits of technology
Problems solved by technology
Method used
Image
Examples
Embodiment Construction
[0031]The benefits and advantages of a two-step RFF assembly in accordance with the present invention may be better appreciated by first considering a prior art two-step RFF assembly.
[0032]Referring to FIG. 1, prior art two-step RFF assembly 10 is substantially as shown in U.S. Pat. No. 6,755,167 B2. Pallet end 12 of prior art RFF 10 is provided for engaging a valve stem 11 and socket end 14 is provided for engaging the hemispherical head of a hydraulic lash adjuster 15. RFF 10 includes body assembly 16, slider arm assembly 18, spool roller assembly 20, lost motion spring 22, and latch assembly 24.
[0033]Body assembly 16 includes elongate body 26 and roller bearing 28 disposed in bearing orifices 30. Elongate body 26 includes a slider arm aperture 32 bounded by body side walls 34 defining bearing orifice 30 therethrough. The diameter of bearing orifice 30 is sized to press-fittedly receive roller bearings 28. A cross-shaft 36 is rotatably disposed in bearing 28 and is supportive of r...
PUM
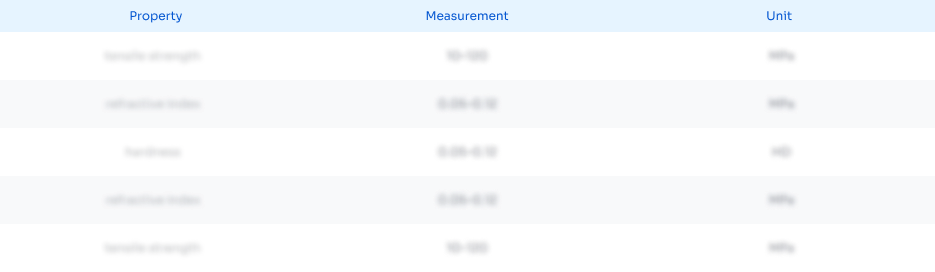
Abstract
Description
Claims
Application Information

- R&D
- Intellectual Property
- Life Sciences
- Materials
- Tech Scout
- Unparalleled Data Quality
- Higher Quality Content
- 60% Fewer Hallucinations
Browse by: Latest US Patents, China's latest patents, Technical Efficacy Thesaurus, Application Domain, Technology Topic, Popular Technical Reports.
© 2025 PatSnap. All rights reserved.Legal|Privacy policy|Modern Slavery Act Transparency Statement|Sitemap|About US| Contact US: help@patsnap.com