Rodless modular conveyor belt
a conveyor belt and modular technology, applied in the direction of conveyors, transportation and packaging, etc., can solve the problem of slipping of the post, and achieve the effect of greater interconnection and greater tensile strength
- Summary
- Abstract
- Description
- Claims
- Application Information
AI Technical Summary
Benefits of technology
Problems solved by technology
Method used
Image
Examples
first embodiment
[0024]In the drawings, FIG. 1 shows in a first embodiment a portion of a belt 10 according to the invention, wherein adjacent modules 12 and 14, or module rows, are retained together along a hinge line 16 without connecting rods or pins. Connection between adjacent module rows is effected with pivot posts 18 which are integrally molded with the modules, extending laterally from projections or knuckles 20. These projections 20 extend as a set of essentially similar projections in one direction from a center section 22 of the module, and another group or set of projections 24 extend in the opposition direction, both along the line of the direction of travel. Herein and in the claims the term “first projections” is often applied to the projections 20, and the term “second projections” or “second set of projections” is often applied to the projections 24. However, this is not to imply any particular direction of travel; if there is a preferred direction of travel, either the projections...
second embodiment
[0030]the rodless conveyor belt of the invention is shown in FIGS. 5 through 12. In this form of the invention the modules 40 have first and second groups of link ends or projections 42 and 44 that are not tapered. Again, this is preferably a solid top conveyor belt as shown, for straight travel. The belt portion 45 shown in FIGS. 5 and 6 is for illustration only, and the belt may be assembled in any desired length and a wide variety of widths, as in the above-described embodiment. In FIG. 6 module row ends, to be positioned at an edge of the belt, are shown on the modules 40. In a belt of single-module rows, these closing ends 46 will be present at each module end, but in the typical wider belt, the modules of adjacent rows will be interleaved or “brick-laid” such that joints between laterally adjacent modules are staggered rather than contiguous from row to row.
[0031]As seen in the drawings, the non-tapered link ends or projections 42 and 44 are assembled somewhat similarly to the...
PUM
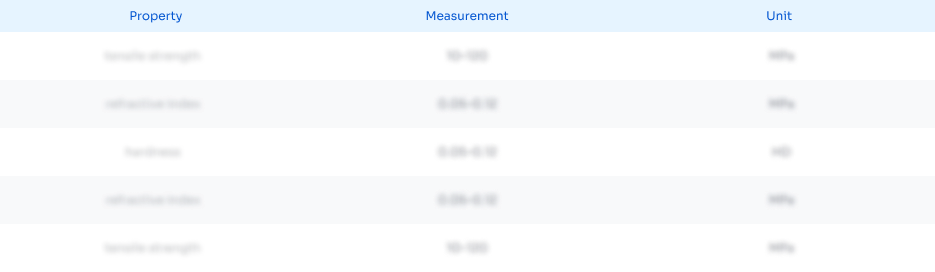
Abstract
Description
Claims
Application Information

- R&D
- Intellectual Property
- Life Sciences
- Materials
- Tech Scout
- Unparalleled Data Quality
- Higher Quality Content
- 60% Fewer Hallucinations
Browse by: Latest US Patents, China's latest patents, Technical Efficacy Thesaurus, Application Domain, Technology Topic, Popular Technical Reports.
© 2025 PatSnap. All rights reserved.Legal|Privacy policy|Modern Slavery Act Transparency Statement|Sitemap|About US| Contact US: help@patsnap.com