Hydraulic rotary motor
a rotary motor and rotary motor technology, applied in the direction of rotary or oscillating piston engines, rotary piston engines, engine lubrication, etc., can solve the problems of large axial construction length of motors and relatively high production and assembly effort, and achieve the effect of small
- Summary
- Abstract
- Description
- Claims
- Application Information
AI Technical Summary
Benefits of technology
Problems solved by technology
Method used
Image
Examples
Embodiment Construction
[0043]The rotary motor 1 shown in FIG. 1 comprises a substantially cup-shaped housing 2 which consists in the drawn embodiment substantially of three parts, namely the motor head 3, the rotor housing ring 4 and the bearing cover 5. As FIG. 1 shows, the bearing cover 5 is set on the rotor housing ring 4 and is screwed via screw connections 6 to the radially projecting flange 7 of the motor head 3 so that an annular rotor gap 8 is formed between the bearing cover 5 and the motor head 3. The ring piston 9 is received in the said rotor gap 8 as is—radially inside this ring piston 9—the substantially likewise disk-shaped rotor 10. In more precise terms, a disk section 11 of a rotor / shaft unit is seated with an exact fit between the bearing cover 5 and the motor head 3. Shaft sections 12 and 13 are shaped in a projecting manner at both sides of the disk section 11 and their outer periphery runs with an exact fit on inner peripheral surfaces of the bearing cover 5 or of the motor head 3.
[0...
PUM
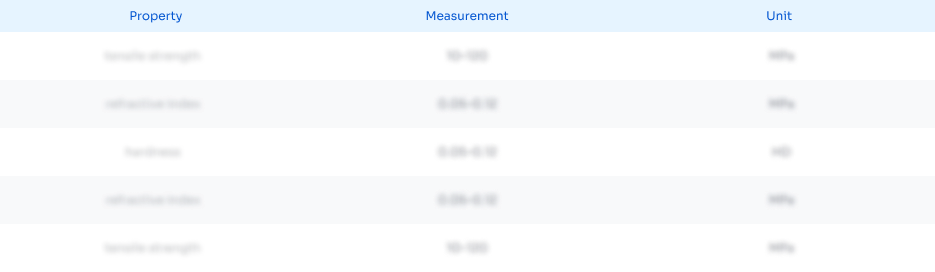
Abstract
Description
Claims
Application Information

- R&D
- Intellectual Property
- Life Sciences
- Materials
- Tech Scout
- Unparalleled Data Quality
- Higher Quality Content
- 60% Fewer Hallucinations
Browse by: Latest US Patents, China's latest patents, Technical Efficacy Thesaurus, Application Domain, Technology Topic, Popular Technical Reports.
© 2025 PatSnap. All rights reserved.Legal|Privacy policy|Modern Slavery Act Transparency Statement|Sitemap|About US| Contact US: help@patsnap.com