Electromagnetically Driven Valve
- Summary
- Abstract
- Description
- Claims
- Application Information
AI Technical Summary
Benefits of technology
Problems solved by technology
Method used
Image
Examples
first embodiment
[0030] The electromagnetically driven valve according to the present embodiment implements an engine valve (an intake valve or an exhaust valve) in an internal combustion engine such as a gasoline engine or a diesel engine. In the present embodiment, description will be given assuming that the electromagnetically driven valve implements an intake valve, however, it is noted that the electromagnetically driven valve is similarly structured also when it implements an exhaust valve.
[0031] Referring to FIG. 1, an electromagnetically driven valve 10 is a rotary drive type electromagnetically driven valve. As an operation mechanism for the electromagnetically driven valve, a parallel link mechanism is applied.
[0032] Electromagnetically driven valve 10 includes a driven valve 14 having a stem 12 extending in one direction, a lower disc 20 and an upper disc 30 coupled to different positions on stem 12 and oscillating by receiving electromagnetic force and elastic force applied thereto, a ...
second embodiment
[0060] An electromagnetically driven valve according to the present embodiment is structured in a manner basically similar to electromagnetically driven valve 10 in the first embodiment. Therefore, description of a redundant structure will not be repeated.
[0061]FIG. 11 shows a region similar to that shown in FIG. 5. Referring to FIG. 11, in the present embodiment, outer circumferential surface 4a of fix portion 4 is formed as a tapered surface. In other words, outer circumferential surface 4a extends in a manner inclined with respect to central axis 25, and is implemented by a side surface of a frustum of a cone formed along central axis 25. On the inner wall of opening 52, a tapered surface being in surface contact with outer circumferential surface 4a while lower torsion bar 26 is inserted in opening 52 is formed. Fix portion 4 has a hexagonal hole 84 formed from a side of an end surface 4c of fix portion 4.
[0062] Disc support base 51 has a female screw hole 81 formed, which is ...
third embodiment
[0069] An electromagnetically driven valve according to the present embodiment is structured in a manner basically similar to electromagnetically driven valve 10 in the first embodiment. Therefore, description of a redundant structure will not be repeated.
[0070]FIG. 13 shows a region similar to that shown in FIG. 5. Referring to FIG. 13, in the present embodiment, outer circumferential surface 4a of fix portion 4 has a male screw formed. Fix portion 4 has a hexagonal hole 88 formed from a side of end surface 4c of fix portion 4. On the other hand, the inner wall of opening 52 has a female screw formed, into which a male screw formed on outer circumferential surface 4a is screwed. A locknut 86 is fastened to opening 52 from a side opposite to fix portion 4, and end surface 4c of fix portion 4 is pressed by an end surface 86c of locknut 86 facing end surface 4c. Locknut 86 has a hole 87 formed, which is penetrated in a direction in which central axis 25 extends.
[0071] The step of ad...
PUM
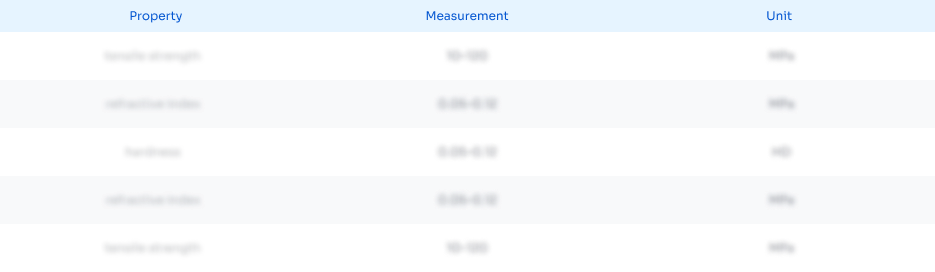
Abstract
Description
Claims
Application Information

- R&D
- Intellectual Property
- Life Sciences
- Materials
- Tech Scout
- Unparalleled Data Quality
- Higher Quality Content
- 60% Fewer Hallucinations
Browse by: Latest US Patents, China's latest patents, Technical Efficacy Thesaurus, Application Domain, Technology Topic, Popular Technical Reports.
© 2025 PatSnap. All rights reserved.Legal|Privacy policy|Modern Slavery Act Transparency Statement|Sitemap|About US| Contact US: help@patsnap.com