Multi-layer heating element
- Summary
- Abstract
- Description
- Claims
- Application Information
AI Technical Summary
Benefits of technology
Problems solved by technology
Method used
Image
Examples
Embodiment Construction
[0024] The present invention, as illustrated in FIGS. 2-5, is directed to a heating element 10 having an electrically insulative layer 20, formed from an electrically insulative material, and an electrically conductive layer 30, formed from an electrically conductive material. As illustrated in FIG. 2, the conductive material is attached to a first electrical contact 40 and a second electrical contact 42 which allow electrical current to flow through the conductive material to generate heat that is primarily focused where the thickness of the conductive layer 30 is at its thinnest point and has the smallest cross cross-sectional area. Although only FIG. 2 is illustrated with the electrical contacts, 40 and 42, the heating element 10 will be generally formed with electrical contacts, which may vary in size, shape and configuration. The heating element also may include a base portion 14 formed in a variety of configurations and shapes.
[0025] The insulative layer 20 further includes a...
PUM
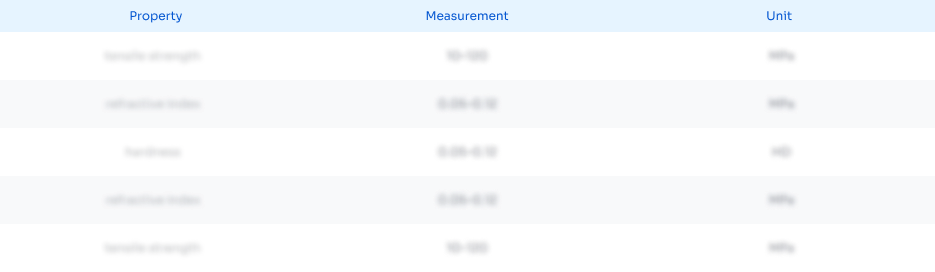
Abstract
Description
Claims
Application Information

- R&D
- Intellectual Property
- Life Sciences
- Materials
- Tech Scout
- Unparalleled Data Quality
- Higher Quality Content
- 60% Fewer Hallucinations
Browse by: Latest US Patents, China's latest patents, Technical Efficacy Thesaurus, Application Domain, Technology Topic, Popular Technical Reports.
© 2025 PatSnap. All rights reserved.Legal|Privacy policy|Modern Slavery Act Transparency Statement|Sitemap|About US| Contact US: help@patsnap.com