Method and device for the combustion of fuel
a fuel combustion and fuel technology, applied in the direction of burners, combustion types, combustion processes, etc., can solve the problems of limited nox formation and relative limited nox formation in this region
- Summary
- Abstract
- Description
- Claims
- Application Information
AI Technical Summary
Benefits of technology
Problems solved by technology
Method used
Image
Examples
Embodiment Construction
[0021] A device 10 for the combustion of fuel in a combustion chamber is illustrated in FIG. 1 in the form of a burner for a stationary gas turbine. An essential component of the device 10 is a combustion chamber 12 which is essentially designed in the form of a circular cylinder along an axis 14. The combustion chamber 12 is formed to include a first end wall 16 which is shown at the top in FIG. 1, an outer wall 18 which extends downwards from said face wall, and a second face wall 20 which is shown at the bottom in FIG. 1.
[0022] A centrally arranged body 22, which essentially has the form of a circular cylinder and likewise extends along the axis 14, passes through the first face wall 16. The body 22 is configured to include an outer tube 24 and an inner tube 26 which is arranged concentrically therein. Nozzles 28 which are oriented radially outwards pass though the outer tube 24, and are located at the lower end region of the outer tube 24 with reference to FIG. 1. The outer tub...
PUM
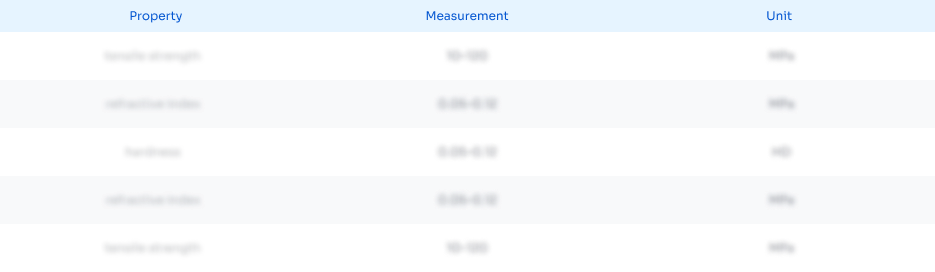
Abstract
Description
Claims
Application Information

- R&D
- Intellectual Property
- Life Sciences
- Materials
- Tech Scout
- Unparalleled Data Quality
- Higher Quality Content
- 60% Fewer Hallucinations
Browse by: Latest US Patents, China's latest patents, Technical Efficacy Thesaurus, Application Domain, Technology Topic, Popular Technical Reports.
© 2025 PatSnap. All rights reserved.Legal|Privacy policy|Modern Slavery Act Transparency Statement|Sitemap|About US| Contact US: help@patsnap.com