Substrate processing apparatus, control method adopted in substrate processing apparatus and program
a substrate processing and control method technology, applied in the direction of electric heating, electric discharge heating, electric apparatus, etc., can solve the problems of reducing the service life of the scrubbing device, reducing reducing the quantity of discharge gas discharged from the processing chamber, so as to reduce the onus on the scrubbing device, reduce the onus on the scrubbing means, and reduce the effect of the scrubbing discharge gas
- Summary
- Abstract
- Description
- Claims
- Application Information
AI Technical Summary
Benefits of technology
Problems solved by technology
Method used
Image
Examples
Embodiment Construction
[0053] The following is a detailed explanation of preferred embodiments of the present invention, given in reference to the attached drawings. It is to be noted that in the specification and the drawings, the same reference numerals are assigned to components having substantially identical functions and structural features to preclude the necessity for a repeated explanation thereof.
[0054] (Structural Example Adopted in Substrate Processing Apparatus)
[0055] First, the substrate processing apparatus achieved in an embodiment of the present invention is explained in reference to drawings. FIG. 1 schematically shows the structure adopted in the substrate processing apparatus in an embodiment of the present invention. The substrate processing apparatus 100 comprises a processing unit 110 where various types of processing such as film formation and etching are executed on substrates which may be, for instance, semiconductor wafers (hereafter may be simply referred to as “wafers”) W and...
PUM
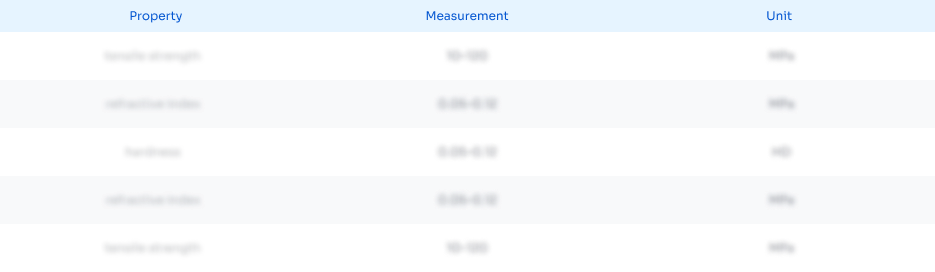
Abstract
Description
Claims
Application Information

- R&D
- Intellectual Property
- Life Sciences
- Materials
- Tech Scout
- Unparalleled Data Quality
- Higher Quality Content
- 60% Fewer Hallucinations
Browse by: Latest US Patents, China's latest patents, Technical Efficacy Thesaurus, Application Domain, Technology Topic, Popular Technical Reports.
© 2025 PatSnap. All rights reserved.Legal|Privacy policy|Modern Slavery Act Transparency Statement|Sitemap|About US| Contact US: help@patsnap.com