Radiation detector and a method of manufacturing the detector
a technology of a detector and a manufacturing method, applied in the field of radiation detectors, can solve the problems of reducing the capability of discriminating and thus detecting, the position of incidence of gamma rays, and the complexity of the manufacturing process, so as to avoid the effect of lowering the resolution
- Summary
- Abstract
- Description
- Claims
- Application Information
AI Technical Summary
Benefits of technology
Problems solved by technology
Method used
Image
Examples
Embodiment Construction
[0041] A preferred embodiment of this invention will be described in detail hereinafter with reference to the drawings.
[0042]FIG. 3 is a view (side view) showing an outward appearance, in an X-direction seen from a Y-direction, of a radiation detector in one embodiment of this invention. FIG. 4 is a view (front view) showing an outward appearance, in the Y-direction seen from the X-direction, of the radiation detector;
[0043] The radiation detector RDA in this embodiment includes a scintillator array 10, a light guide 20 optically combined to the scintillator array 10, and four photomultiplier tubes 301, 302, 303 and 304 optically combined to the light guide 20. FIG. 3 shows the photomultiplier tube 301 and photomultiplier tube 302. FIG. 4 shows the photomultiplier tube 301 and photomultiplier tube 303.
[0044] The scintillator array 10 has scintillators 1S in a compact, two-dimensional arrangement, the scintillators 1S being defined by light reflecting elements 11 and light transmi...
PUM
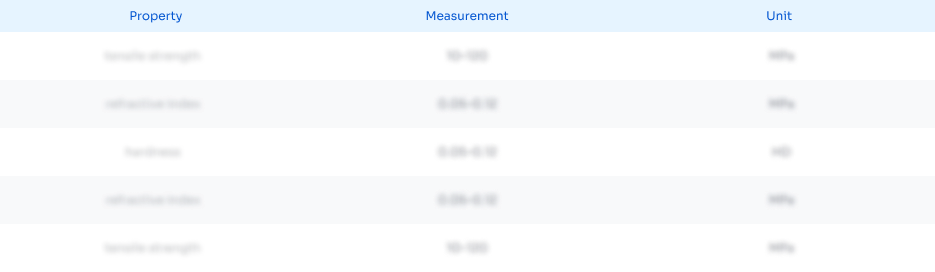
Abstract
Description
Claims
Application Information

- R&D
- Intellectual Property
- Life Sciences
- Materials
- Tech Scout
- Unparalleled Data Quality
- Higher Quality Content
- 60% Fewer Hallucinations
Browse by: Latest US Patents, China's latest patents, Technical Efficacy Thesaurus, Application Domain, Technology Topic, Popular Technical Reports.
© 2025 PatSnap. All rights reserved.Legal|Privacy policy|Modern Slavery Act Transparency Statement|Sitemap|About US| Contact US: help@patsnap.com