Animal sorting and grading system using MRI to predict maximum value
a grading system and animal technology, applied in the field of animal grading system using mri to predict maximum value, can solve the problems of not finding the correct 30 animals, several days of no weight gain for the remaining 270 animals, and too much fat, so as to reduce, if not eliminate, the dollar loss
- Summary
- Abstract
- Description
- Claims
- Application Information
AI Technical Summary
Benefits of technology
Problems solved by technology
Method used
Image
Examples
Embodiment Construction
, Belk thoroughly explains the use of a color video IA system to determine palatability and yield. He also provides a very limited and very brief explanation of the use of tomographics (CAT or PET) and ultrasound for his (IA) system to secure the palatability and yield results. Belk fails to describe in any manner the means by which the MRI would be used in his image analysis (IA) system and makes no attempt to explain the method or means in which MRI could determine or provide palatability and yield predictions of meat. Additionally, Belk fails to explain that one advantage of MRI technology is the fact that the carcass does not need to be severed to attain intramuscular fat distribution, I. Fat percentages and ribeye surface area measurements that are used in part to determine palatability and yield.
[0026] It is thus apparent that there is a need in the art for an improved process for comparing, sorting and grading animals in to groups of like kinds by evaluating and predicting a ...
PUM
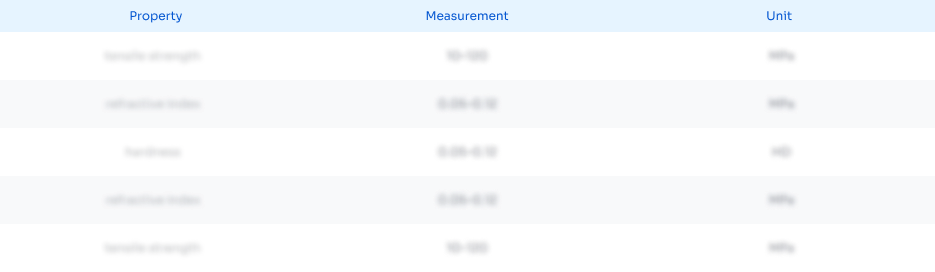
Abstract
Description
Claims
Application Information

- R&D
- Intellectual Property
- Life Sciences
- Materials
- Tech Scout
- Unparalleled Data Quality
- Higher Quality Content
- 60% Fewer Hallucinations
Browse by: Latest US Patents, China's latest patents, Technical Efficacy Thesaurus, Application Domain, Technology Topic, Popular Technical Reports.
© 2025 PatSnap. All rights reserved.Legal|Privacy policy|Modern Slavery Act Transparency Statement|Sitemap|About US| Contact US: help@patsnap.com