Fastening assemblies and components thereof
a technology of fastening assemblies and components, applied in the direction of fastening means, fastening tools, sheet joining, etc., can solve the problems of difficult to tell which fastening assemblies the studs belong to, low clearance required to remove a panel, and many existing captive fastening assemblies are also quite delica
- Summary
- Abstract
- Description
- Claims
- Application Information
AI Technical Summary
Benefits of technology
Problems solved by technology
Method used
Image
Examples
Embodiment Construction
[0072] The present disclosure is directed to a fastening assembly that may be used in high stress environments for attaching a cover to a panel, such as covers used to close access openings in panels of an aircraft. In some embodiments, the present fastening assemblies may include stud assemblies that allow the stud to be positioned in several predetermined extended positions while remaining captive within the stud assembly. Such a feature is useful, for example, when curved covers are attached to curved panels using a plurality of fastening assemblies, each of which may require different stud clearances in order to remove the cover from the panel. In some embodiments, the fastening assembly may include a nut that provides even distribution of stress along the nut. In other embodiments, the fastening assembly may be configured and dimensioned to be attached to a panel using a single bolt or rivet, which allows the fastening assembly to be used in otherwise inaccessible regions. In o...
PUM
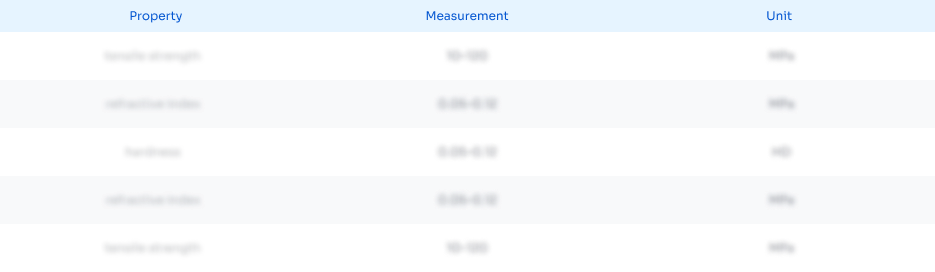
Abstract
Description
Claims
Application Information

- R&D
- Intellectual Property
- Life Sciences
- Materials
- Tech Scout
- Unparalleled Data Quality
- Higher Quality Content
- 60% Fewer Hallucinations
Browse by: Latest US Patents, China's latest patents, Technical Efficacy Thesaurus, Application Domain, Technology Topic, Popular Technical Reports.
© 2025 PatSnap. All rights reserved.Legal|Privacy policy|Modern Slavery Act Transparency Statement|Sitemap|About US| Contact US: help@patsnap.com