Foam cushion and method of making and using the same
a foam cushion and foam technology, applied in the field of foam cushion and method of making and using the same, can solve the problems of many carpet paddings that move so much up and down, and many carpet paddings do not effectively repel liquid and moisture, etc., to achieve suitable shock absorption and thermal insulation properties, and reduce manufacturing costs
- Summary
- Abstract
- Description
- Claims
- Application Information
AI Technical Summary
Benefits of technology
Problems solved by technology
Method used
Examples
examples
[0118] Following the General Procedure as outlined below, an article of manufacture can be produced.
General Procedure:
[0119] (1) Mix the following substances together: at least one or a resin (colored or colorless) and rubber; a blowing agent (optional), a polymeric adhesion modifier (optional), a decomposition accelerating agent (optional), a cross-linking agent (optional), and one or more auxiliary materials (optional) to form a Concentrated Batch and heat (optional) for a period of time; [0120] (2) Cut the Concentrated Batch into desired Lumps; [0121] (3) Thin the Lumps into thin Sheets of desired thickness; [0122] (4) Cool (to room temperature) Sheets (optional); [0123] (5) Cut Sheets to specific length Pieces (optional); [0124] (6) Spray Non-Stick Substance (optional) to all surfaces of the (optionally textured) Press Mold; [0125] (7) Layer a desired number of Pieces to form a Stack in Press Mold; [0126] (8) Cook Stack in Press; [0127] (9) Remove Cooked Stack from Press Mold...
example # 1
Example #1
[0147] (1) Mix:
[0148] 44.86 Kg Ethylene Vinyl Acetate (White Colored),
[0149] 4.49 Kg Rubber,
[0150] 2.06 Kg Vinyfor AC 7,
[0151] 1.79 Kg Fusabond,
[0152] 0.90 Kg Zinc Oxide, and
[0153] 0.54 Kg Stearic Acid,
[0154] at 100° C.-130° C. for 15 Minutes; and mix
[0155] 0.36 Kg Dicumyl Peroxide at 110° C.-130° C. for 3 minutes;
[0156] mix at 100° C.-130° C. until concentrated to 20 mm thickness. [0157] (2) Cut (1) to 2 Kg Lumps and mix separately at 80° C.-100° C. [0158] (3) Thin Lumps into 1 mm Sheets 6 Ft Width by 7.5 Ft Length. [0159] (4) Cool Sheets slowly to room temperature with non-contact water cooling system. [0160] (5) Cut Sheets to Pieces 6 Width by 7.5 Ft Length. [0161] (6) Apply Silicone Spray to all surfaces of the textured Press Mold. [0162] (7) Layer 50 Pieces in Height in Adjacent Stacks to form an Adjoined Pre-Cooked Stack centered in the Press Mold (with the interior perimeter of the Press Mold exposed up to 50.0% of the surface area). [0163] (8) Cook Stack i...
example # 2
Example #2
[0172] (1) Mix 44.86 Kg Ethylene Vinyl Acetate—White Colored,
[0173] 4.49 Kg Rubber,
[0174] 2.06 Kg Vinyfor AC 7,
[0175] 1.79 Kg Fusabond,
[0176] 0.90 Kg Zinc Oxide, and
[0177] 0.54 Kg Stearic Acid,
[0178] at 110° C.-130° C. for 15 Minutes; and mix
[0179] 0.36 Kg Dicumyl Peroxide at 110° C.-130° C. for 3 Minutes;
[0180] mix at 100° C.-130° C. until concentrated to 20 mm thickness. [0181] (2) Cut (1) to 2 Kg Lumps and mix separately at 80° C.-100° C. [0182] (3) Thin Lumps into 1 mm Sheets 6 Ft Width by 7.5 Ft Length. [0183] (4) Cool Sheets slowly to room temperature with non-contact water cooling system. [0184] (5) Cut Sheets to Pieces 6 Ft Width) by 7.5 Ft Length. [0185] (6) Apply Silicone Spray to all surfaces of the Press Mold. [0186] (7) Layer 50 Pieces in Height in Adjacent Stacks to form an Adjoined Pre-Cooked Stack centered in the Press Mold (with interior perimeter of the Press Mold exposed up to 50.0% of the surface area). [0187] (8) Cook Stack in Press for 28-35 M...
PUM
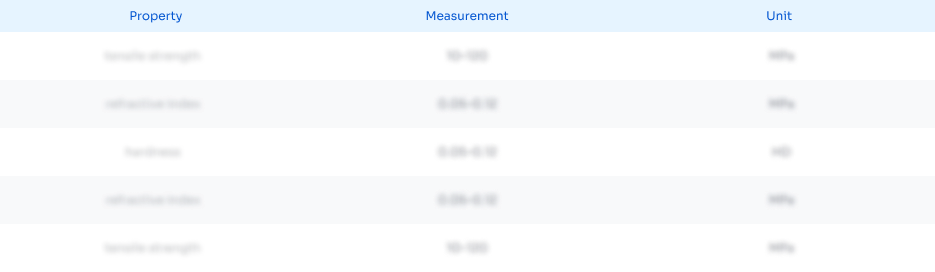
Abstract
Description
Claims
Application Information

- R&D
- Intellectual Property
- Life Sciences
- Materials
- Tech Scout
- Unparalleled Data Quality
- Higher Quality Content
- 60% Fewer Hallucinations
Browse by: Latest US Patents, China's latest patents, Technical Efficacy Thesaurus, Application Domain, Technology Topic, Popular Technical Reports.
© 2025 PatSnap. All rights reserved.Legal|Privacy policy|Modern Slavery Act Transparency Statement|Sitemap|About US| Contact US: help@patsnap.com