Flavorful low-fat and reduced fat cheese
- Summary
- Abstract
- Description
- Claims
- Application Information
AI Technical Summary
Benefits of technology
Problems solved by technology
Method used
Image
Examples
example 1
Preliminary Experiments on Mozzarella Cheese
Water was removed from Mozzarella cheese during the first two weeks of refrigerated storage by grinding, warming, and centrifuging the cheese to remove water. After about 10 to 12 days, water could no longer be removed from the cheese by centrifugation at 25° C. However, as the Mozzarella cheese got older, an increasing amount of fat could be removed. Aged Cheddar cheese was used to further develop a method for physically removing fat to produce reduced fat aged Cheddar cheeses.
example 2
Preliminary Experiments on Cheddar Cheese
Test batches of lower fat Cheddar cheese containing about 25 to 60% less fat were made by removing butter oil from both commercial and university produced full fat aged Cheddar cheese. In general, about 25% of the fat was removed from aged Cheddar cheese by warming the cheese to about 22° C. and centrifuging it at about 24,000 g for 20 minutes. Twenty minutes of centrifugation is probably longer than what was needed under the shredding and warming conditions used. At a warming temperature of about 30° C., a significant amount of butter oil had already leaked out of the cheese before centrifugation, and about 50% of fat could be removed after centrifugation. At 37° C., a 62% fat reduction was achieved.
Starting with an aged Cheddar cheese of about 34% fat and 36.5% moisture, fat separation at 30° C. resulted in a final composition of 16% fat and 45.6% moisture. When fat is removed, it is normal for the percentage of both moisture and protei...
example 3
Temperature Influences Fat Removal
Materials and Methods
Commercial aged Sharp Cheddar cheese was used as a starting material. The cheese was shredded to a diameter of about 4 mm at a temperature of about 4 to 6° C. After shredding, the cheese was warmed to a temperature between 20° C. and 37° C. A Sorval centrifuge with a GSA centrifuge head and a 250 ml capacity screw cap centrifuge tubes were used for separating the butter oil from the bulk of the cheese. The centrifugal force was varied from 800 to 24,000×g for times ranging from 5 to 25 minutes to test for the effect of centrifugal force and duration on butter oil removal. The butter oil was decanted from the centrifuge tubes. The lower layer of reduced fat cheese solids was removed, blended to make it homogeneous, adjusted to various target moisture levels (e.g., 48%, 50%, 52%, etc.) and pressed into small blocks (about 2.5 lbs).
Results
FIG. 1 illustrates the amount of fat removed at different temperatures as a function of...
PUM
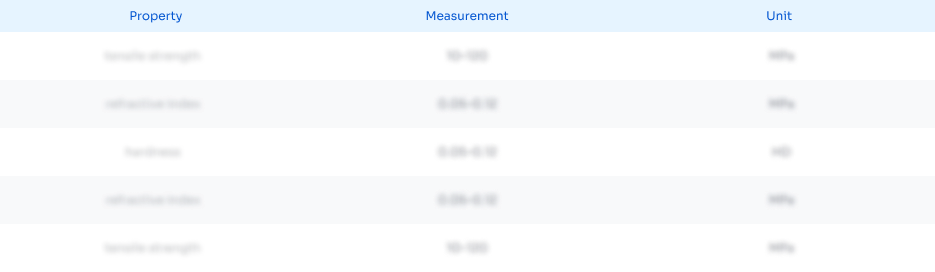
Abstract
Description
Claims
Application Information

- R&D
- Intellectual Property
- Life Sciences
- Materials
- Tech Scout
- Unparalleled Data Quality
- Higher Quality Content
- 60% Fewer Hallucinations
Browse by: Latest US Patents, China's latest patents, Technical Efficacy Thesaurus, Application Domain, Technology Topic, Popular Technical Reports.
© 2025 PatSnap. All rights reserved.Legal|Privacy policy|Modern Slavery Act Transparency Statement|Sitemap|About US| Contact US: help@patsnap.com