Apparatus for and method of installing subsea components
a technology for installing subsea components and accessories, which is applied in the field of accessories for and methods of installing subsea components, can solve the problems of ahts vessels, ahts-type vessels, and the cost of using derreks and crane barges can be as much as 3 to 10 times more expensive per day, so as to reduce the potential for components to bounce and reduce the effect of heaving
- Summary
- Abstract
- Description
- Claims
- Application Information
AI Technical Summary
Benefits of technology
Problems solved by technology
Method used
Image
Examples
example 1
[0044] The vessel 10 is an AHTS of at least 90 meters long, 23,480 BHP of main engine power and continuous bollard pull of 250 tons and having the following characteristics:
[0045] LOA=90.30 meters, Beam=23.00 meters, Depth=9.50 meters;
[0046] 17280 kW (23480 BHP) main propulsion engines;
[0047] 2.times.880 kW stern thrusters, 1.times.1500 kW bow thruster and 1.times.1300 kW retractable azimuth type bow thruster;
[0048] DP (AA) under Lloyd's Class (DP Class II);
[0049] Triple drum anchor handling & towing winch, maximum pull capacity 400 tonnes and 625 tons depending on drum.
[0050] 2 chain handling systems and 4.times.250 cubic meter chain lockers;
[0051] 2 sets of 700 tons shark jaws with towing / guide pins;
[0052] Two 4.0 meters diameter stern rollers, rated at 800 tons each;
[0053] 60 person accommodations; and
[0054] Two complete 100 hp ROV systems, one of which will be the back-up system. The ROV systems are mounted on separate platforms above the vessel's main deck.
[0055] The capacity o...
example 2
[0072] In order to theoretically calculate nitrogen pressure before starting operation when motion compensator is filly retracted, the below procedure can be followed:
[0073] 1. Determine the weight of load into water.
[0074] 2. Draw the isothermic curve from the central point
[0075] X=2 m
[0076] Y=above load
[0077] Calculate the corresponding POVO at X=0 m (retracted position)
P.sub.0V.sub.0=P.sub.1V.sub.1.times.P.sub.2V.sub.2
[0078] When
[0079] V.sub.0=Nitrogen Volume when fully retracted
[0080] =3.times.353+640=1700 liters
[0081] V.sub.1=Nitrogen Volume when mi-extended
[0082] =3.times.353+320=1380 liters
[0083] P.sub.1=Pressure at mid-extended
[0084] =Load / 1.583
[0085] V.sub.2=Nitrogen Volume when fully extended
[0086] =3.times.353=1060 liters
[0087] P.sub.0 is the Nitrogen pressure when fully retracted.
[0088] 3. Draw the adiabatic curves using the above procedure but with a polytropic exponent n=1.4
P.sub.0V.sub.0.sup.1.4=P.sub.1V.sub.1.sup.1.4=P.V..sup.1.4
[0089] Nitrogen Pressure Selection
2 In...
example 3
[0094] Torque values generally quoted are maximum values and are given at a load equal to 20% of the breaking strength (FOS=5). Some ropes will have non-linear torque to load curves. It is generally assumed that the rope is torque-free when unloaded. Torque is maximum on a new rope. Wear and usage diminishes the torque value, improving stability. These calculations may be conservative in other ways.
[0095] For example, if the increase in load is due to the weight of the wire, the incremental increase in rotation should be half the value that would be caused by increasing the component's 22 weight by the same amount.
[0096] Weight of manifold: W:=927.multidot.kip
[0097] Should include wire and spreader beam too. Term cancels out later in analysis.
[0098] Nominal rope diameter: d:=3.multidot.in
[0099] Number of parts: n:=2
[0100] Torque generated per part of sheave line: 1 T part := T fac 1 W n d T part = 8111.25 lb ft
[0101] Total torque generate by two-parts, an upper block or T.sub.tot:=n...
PUM
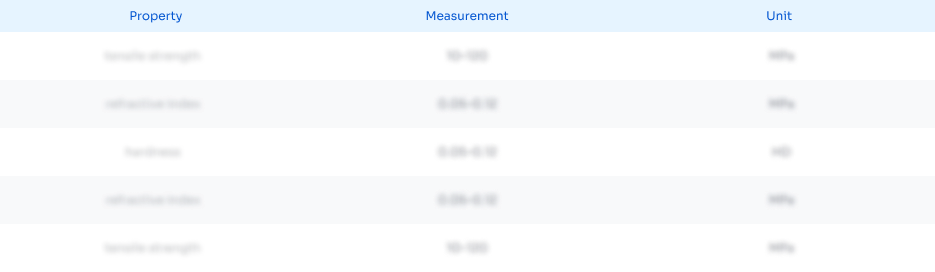
Abstract
Description
Claims
Application Information

- R&D
- Intellectual Property
- Life Sciences
- Materials
- Tech Scout
- Unparalleled Data Quality
- Higher Quality Content
- 60% Fewer Hallucinations
Browse by: Latest US Patents, China's latest patents, Technical Efficacy Thesaurus, Application Domain, Technology Topic, Popular Technical Reports.
© 2025 PatSnap. All rights reserved.Legal|Privacy policy|Modern Slavery Act Transparency Statement|Sitemap|About US| Contact US: help@patsnap.com