Carbon fiber mixing reinforced magnesium-base high modulus composite material and its preparing process
A composite material and carbon fiber technology, applied in the field of composite material technology preparation, can solve the problems of complex preparation process, difficult large-scale application, and high equipment requirements, and achieve the effects of simple process, low production cost, and simple preparation method.
- Summary
- Abstract
- Description
- Claims
- Application Information
AI Technical Summary
Problems solved by technology
Method used
Examples
Embodiment 1
[0024] The carbon fibers used are produced by Jilin Carbon Plant, with a diameter of 6-8 μm, each bundle of carbon fibers has 1000 monofilaments, and a modulus of 175GPa. The carbon fiber is three-dimensionally woven into a prefabricated part, and the weaving density (the volume of the fiber before weaving to the volume of the prefabricated part after weaving) is 30%. Soak the preform in acetone for 5 minutes to remove the glue, take it out, soak it in deionized water for 10 minutes, wash off the residual acetone, and dry it at low temperature at 100°C for 1 hour; take the hollow microspheres and Mix with water, the mass ratio of hollow microspheres is 20%, and stir evenly to obtain a suspension of hollow microspheres; place the carbon fiber prefabricated part in the suspension of hollow microspheres with a mass ratio of 20%, soak and apply 40kHz ultrasonic vibration 15 minutes, take out and dry at 100°C for 60 minutes.
[0025] Preheat the squeeze casting mold to 250°C and t...
Embodiment 2
[0027] Use carbon fiber with embodiment 1. Carbon fibers are three-dimensionally woven into prefabricated parts with a weaving density of 45%. Soak the preform in acetone for 5 minutes to remove the glue, take it out, soak it in deionized water for 10 minutes, wash off the residual acetone, and dry it at low temperature at 125°C for 1 hour; take the hollow microspheres and Mix with water, the mass ratio of hollow microspheres is 15%, and stir evenly to obtain a suspension of hollow microspheres; place the prefabricated carbon fiber in the suspension of hollow microspheres with a mass ratio of 20%, soak and apply 40kHz ultrasonic vibration After 20 minutes, take it out and dry it at 125°C for 50 minutes.
[0028] Preheat the squeeze casting mold to 350°C and the preform to 500°C. Under the condition of gas protection, after pure magnesium and 8% pure aluminum are completely melted at 740°C, add 0.5% Re in the form of Al-10Re, add 2.5% Si in the form of Al-50Si, stir for 10 mi...
Embodiment 3
[0030] Use carbon fiber with embodiment 1. Carbon fiber is three-dimensionally woven into prefabricated parts with a weaving density of 70%. Soak the preform in acetone for 5 minutes to remove the glue, take it out, soak it in deionized water for 10 minutes, wash off the residual acetone, and dry it at low temperature at 150°C for 1 hour; take the hollow microspheres and Mix with water, the mass ratio of hollow microspheres is 10%, and stir evenly to obtain a suspension of hollow microspheres; place the prefabricated carbon fiber in the suspension of hollow microspheres with a mass ratio of 20%, soak and apply 40kHz ultrasonic vibration 30 minutes, take out and dry at 150°C for 30 minutes.
[0031] Preheat the squeeze casting mold to 400°C and the preform to 650°C. Under the condition of gas protection, after pure magnesium and 10% pure aluminum are completely melted at 760°C, add 1% Re in the form of Al-10Re and 5% Si in the form of Al-50Si, stir for 10 minutes, and the sti...
PUM
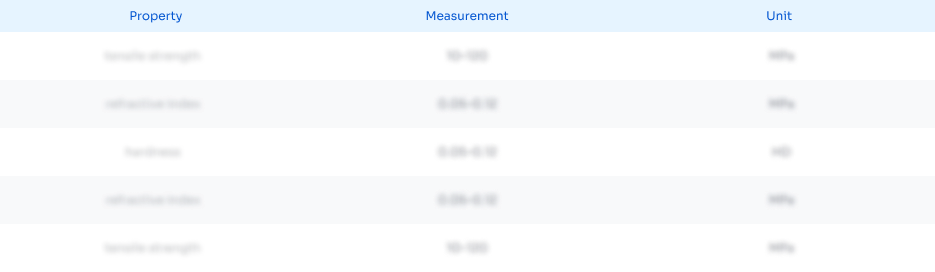
Abstract
Description
Claims
Application Information

- R&D Engineer
- R&D Manager
- IP Professional
- Industry Leading Data Capabilities
- Powerful AI technology
- Patent DNA Extraction
Browse by: Latest US Patents, China's latest patents, Technical Efficacy Thesaurus, Application Domain, Technology Topic, Popular Technical Reports.
© 2024 PatSnap. All rights reserved.Legal|Privacy policy|Modern Slavery Act Transparency Statement|Sitemap|About US| Contact US: help@patsnap.com