Fault diagnosis and fault-tolerant control method for brushless motor position signal
A brushless motor and fault diagnosis technology, applied in the direction of electronic commutator, monitoring commutation, etc., can solve the problem of position signal fault diagnosis and fault-tolerant control not involved, and achieve the effect of improving system reliability and broadening the scope of application.
- Summary
- Abstract
- Description
- Claims
- Application Information
AI Technical Summary
Problems solved by technology
Method used
Image
Examples
Embodiment Construction
[0035] 1 Types of position signal failures
[0036] The three-phase brushless motor needs three position sensors, and the three position sensors have a mutual difference of 120° in space. The position signal generated is shown in Figure 1. The 1 / 3 cycle is high level, and the 2 / 3 cycle is low level. The phase difference between the three position signals is 1 / 3 cycle. Position signal faults can be divided into three types: ① one-phase fault; ② two-phase fault; ③ three-phase fault. Among the three kinds of faults, the probability of failure of one-phase position signal is the highest, followed by two-phase failure, and the lowest failure rate is three-phase failure at the same time. There may be two states after the position signal fails:
[0037] ①Constantly low level, that is, H i ≡0, i=A, B, C;
[0038] ②Constantly high level, that is, H i ≡1, i=A, B, C.
[0039] For four-phase switched reluctance motors such as 8 / 6 poles and double salient poles, two position sensors ...
PUM
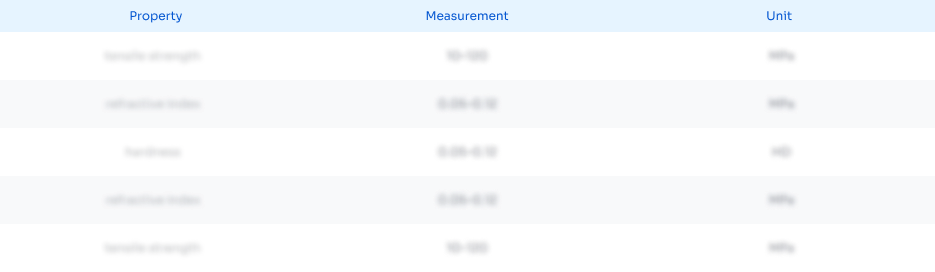
Abstract
Description
Claims
Application Information

- Generate Ideas
- Intellectual Property
- Life Sciences
- Materials
- Tech Scout
- Unparalleled Data Quality
- Higher Quality Content
- 60% Fewer Hallucinations
Browse by: Latest US Patents, China's latest patents, Technical Efficacy Thesaurus, Application Domain, Technology Topic, Popular Technical Reports.
© 2025 PatSnap. All rights reserved.Legal|Privacy policy|Modern Slavery Act Transparency Statement|Sitemap|About US| Contact US: help@patsnap.com