Heat recovery combustion furnace
A heat recovery type, combustion furnace technology, applied in the combustion method, combustion type, incinerator and other directions, can solve the problems of air pollution, VOC waste gas residue, control errors, etc., to reduce air pollution, low manufacturing cost, and simple production. Effect
- Summary
- Abstract
- Description
- Claims
- Application Information
AI Technical Summary
Problems solved by technology
Method used
Image
Examples
Embodiment Construction
[0056] Please refer to FIG. 2 to FIG. 4 . FIG. 2 to FIG. 4 are schematic diagrams of a heat recovery combustion furnace according to a preferred embodiment of the present invention. As shown in FIG. 2 , a heat recovery combustion furnace 30 includes a heat recovery chamber 32 , a heat recovery chamber 34 , and a combustion chamber 36 connected between the heat recovery chamber 32 and the heat recovery chamber 34 . Wherein, the heat recovery chamber 32 includes a regenerator 32a and an empty chamber 32b below the regenerator 32a, and the heat recovery chamber 34 also includes a regenerator 34a and an empty chamber below the regenerator 34a. 34b, the heat storage chambers 32a and 34a are filled with a plurality of heat storage bricks, and the heat storage bricks are usually made of heat storage materials such as stone or ceramics. In addition, a burner 38 is provided in the combustion chamber 36 to maintain the combustion chamber 36 at an appropriate reaction temperature (800° C...
PUM
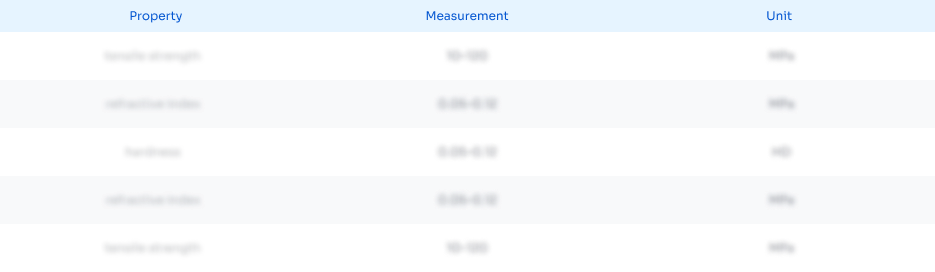
Abstract
Description
Claims
Application Information

- Generate Ideas
- Intellectual Property
- Life Sciences
- Materials
- Tech Scout
- Unparalleled Data Quality
- Higher Quality Content
- 60% Fewer Hallucinations
Browse by: Latest US Patents, China's latest patents, Technical Efficacy Thesaurus, Application Domain, Technology Topic, Popular Technical Reports.
© 2025 PatSnap. All rights reserved.Legal|Privacy policy|Modern Slavery Act Transparency Statement|Sitemap|About US| Contact US: help@patsnap.com